Exploring the Connection Between QMS and LIMS
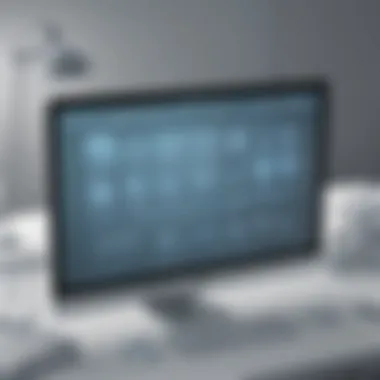
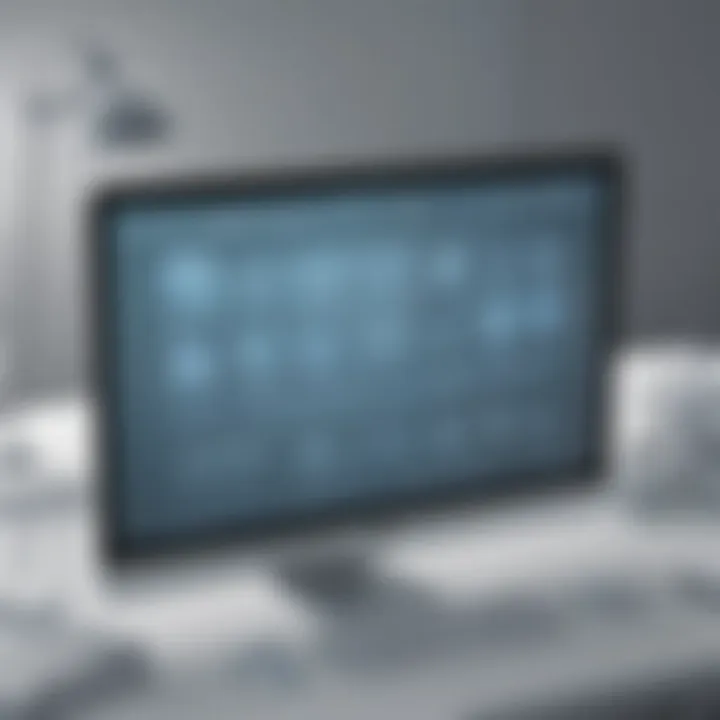
Intro
In the realm of scientific research and production, the efficiency and reliability of operations is paramount. Two systems have become cornerstones in this landscape: Quality Management Systems (QMS) and Laboratory Information Management Systems (LIMS). While each serves unique roles, their integration holds transformative potential for enhancing productivity, ensuring compliance, and maintaining data integrity.
This article aims to dissect the interplay between QMS and LIMS, exploring how they function both independently and in unison to create robust laboratory environments. By revealing their foundational elements, integration opportunities, and collective benefits on operational workflows, we hope to provide an insightful guide for small to medium-sized businesses, entrepreneurs, and IT professionals. Understanding these systems is essential not only for seamless operations but also for navigating the complex regulatory landscape that governs laboratory work.
The following sections will dive into the specifics of these systems, their functionalities, and their roles in driving efficiency and compliance in laboratory settings. Let's begin by examining the foundational principles of these systems.
Intro to QMS and LIMS
In today's competitive landscape, understanding the mechanisms behind Quality Management Systems (QMS) and Laboratory Information Management Systems (LIMS) is crucial for businesses, especially those operating in scientific and technical fields. The interplay of these systems can greatly influence operational efficiency and product quality. This article seeks to unravel the intricacies involved, offering insights that not only pertain to their individual functionalities but also their complementary roles in enhancing organizational effectiveness.
Quality Management Systems are designed to ensure that products and services consistently meet customer requirements. This is significant because a robust QMS fosters an environment of continuous improvement, ultimately benefiting both the business and its customers.
On the flip side, Laboratory Information Management Systems serve as the backbone for managing samples, associated data, and laboratory workflows. They enable labs to track complex processes while ensuring data integrity and compliance with regulatory standards. Together, these systems form a cohesive framework that supports quality assurance and operational excellence.
In this article, we will delve into the definitions and functionalities of QMS and LIMS, explore their unique benefits and the synergy achieved through their integration, and consider various aspects that influence their implementation. The relevance of these systems extends beyond academic knowledge; it directly impacts business decision-making and strategy. This is essential reading for small to medium-sized businesses, entrepreneurs, and IT professionals aiming to grasp how these systems can be leveraged to improve efficiency and compliance.
"An investment in knowledge pays the best interest."
Defining Quality Management Systems
Quality Management Systems, more commonly referred to as QMS, encompass the organizational structure, processes, and resources needed to implement quality management. A QMS is not just a protocol; it's a culture that embeds quality into the very fabric of an organization. It aims to enhance customer satisfaction by ensuring that all products and services meet specified requirements. Various frameworks exist which help in adopting a QMS, such as ISO 9001, which acts as a best-practice guideline across various industries.
The significance of establishing a QMS lies in its ability to standardize processes. This standardization not only improves efficiency but also establishes a consistent quality level, reducing variability in outputs. Moreover, a well-implemented QMS can provide businesses a competitive edge by building customer trust and loyalty.
Businesses can gain insights into performance metrics and areas for improvement by utilizing various tools, such as audits and customer feedback surveys. Overall, a QMS functions as a comprehensive system aiming not just to meet standards but to exceed them.
Understanding Laboratory Information Management Systems
Laboratory Information Management Systems, or LIMS, is software that assists in the management of samples, laboratory workflows, and data ensuring efficient operation of laboratory processes. It effectively organizes information related to samples, tests, and results, creating a streamlined process from sample receipt to report generation.
LIMS allows laboratories to manage a multitude of functions including, but not limited to:
- Sample tracking: Ensuring that every sample is accounted for at all stages of testing.
- Data management: Storing vast amounts of data while maintaining retrievability.
- Compliance management: Providing the necessary tools to help labs meet applicable regulatory standards.
By automating routine tasks, LIMS can reduce human error, saving both time and resources, thus enhancing laboratory efficiency. In addition, the data integrity maintained by LIMS contributes to better decision-making processes, enabling labs to serve their clients more effectively.
The Purpose of Quality Management Systems
Quality Management Systems (QMS) serve a pivotal role in any organizational landscape. Businesses, especially in highly regulated industries like pharmaceuticals or environmental testing, rely on QMS to mitigate risks and enhance operational outputs. The essence of a QMS lies in its structured approach towards achieving specific and measurable quality objectives while cultivating a culture of continuous improvement. This not only assures compliance with established standards but also empowers organizations to consistently deliver premium products and services. By embedding QMS into their core practices, companies make a deliberate move towards operational excellence.
Ensuring Consistency in Quality
Ensuring consistency in quality might sound like a simple expectation, yet it is one of the paramount challenges many businesses face. The hallmark of a robust QMS is its ability to set clear standards and processes. By doing so, organizations can maintain uniformity across their products and services, minimizing variations that could lead to customer dissatisfaction or compliance issues.
For instance, think of a bakery that prides itself on artisan breads. If the baking process is not consistent, the flavors could vary wildly from one batch to the next, disappointing loyal customers and diminishing brand trust. A QMS helps standardize the recipe, baking times, and even the procurement of raw ingredients, ensuring that every loaf is as good as the last. This principle applies universally, whether it’s a tech startup running code reviews or a laboratory conducting tests.
- Standard Operating Procedures (SOPs): Effective QMS requires clear, easily accessible SOPs. These documents act as guiding stars, illuminating the expected pathways for employees to follow.
- Regular Audits and Reviews: Systematic evaluations help identify discrepancies and challenges, ensuring that quality stays on its predetermined track.
- Employee Training Programs: Consistency is only achievable when staff members are well-informed and equipped to perform their roles efficiently. Regular training not only enhances skills but also fosters a shared understanding of quality expectations.
In light of this, organizations can greatly benefit from a systematic QMS, improving both product quality and overall reliability.
Enhancing Customer Satisfaction
Enhancing customer satisfaction forms the cornerstone of any successful business operation. When companies implement a QMS tailored to customer feedback and needs, they not only identify preferences but also refine their offerings accordingly. A noticeable gap in understanding customer expectations can result in products or services that miss the mark, leading to dissatisfaction and possible loss of clientele.
By engaging with customer feedback, a QMS allows businesses to adapt swiftly. For instance, consider a health supplement company that sees a surge in requests for gluten-free options. By actively utilizing their QMS to analyze market trends and customer inquiries, they can pivot, adjusting their product range to include these options seamlessly.
Key benefits of focusing on customer satisfaction through QMS include:
- Improved responsiveness to customer feedback, allowing for timely product modifications.
- Data-driven decision-making based on analysis of customer preferences and behaviors.
- Enhanced brand loyalty, as customers are more likely to return to a business that consistently meets and exceeds their expectations.
Incorporating these principles into a quality management strategy not only elevates the product line but also fosters a loyal customer base, which is invaluable in today’s competitive market landscape.
A well-implemented QMS acts as a bridge between a company's ambitions and customer needs, clearly aligning operational capabilities with market expectations.
By understanding its purpose—ensuring quality consistency and enhancing customer satisfaction—businesses can significantly improve not just their operational efforts but also their long-term viability.
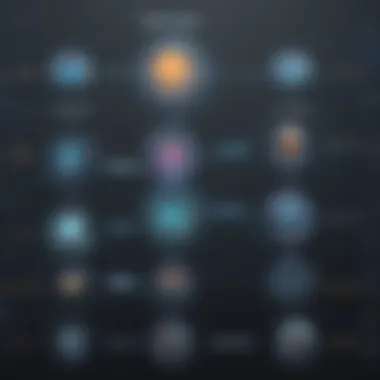
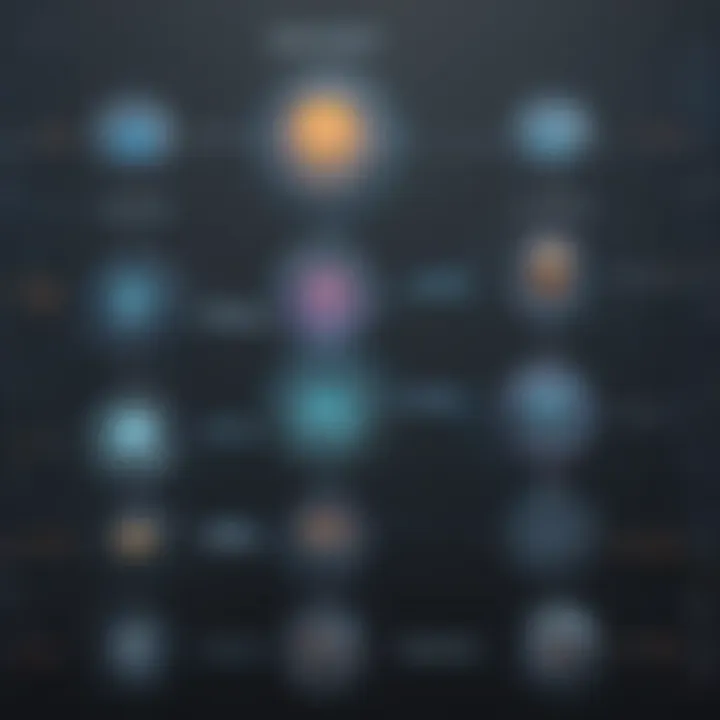
Key Components of a QMS
When discussing Quality Management Systems (QMS), it’s essential to zero in on the components that form the backbone of these systems. Pivotal to ensuring quality in laboratory settings, these components enable organizations to uphold their standards and respond adeptly to varying demands. Each key element plays a distinct yet interwoven role, influencing the overall efficacy of QMS. Understanding these facets can provide a roadmap for businesses looking to enhance their operational framework.
Document Control and Records Management
Document control and records management stand as the cornerstone of any effective QMS. Without rhyme or reason, having robust systems in place to manage documents can save a company from a veritable quagmire of chaos. In essence, this component ensures that all procedures, work instructions, and policies are up-to-date, accurate, and easily accessible.
Importance: Partners with compliance requirements, such as GMP (Good Manufacturing Practices), and facilitates audits by providing a clear record trail. With organized documentation, teams can focus on their core duties rather than rummaging through a sea of paperwork in a frantic search for the latest version of a protocol.
Best Practices:
- Version Control: Always track document revisions to ensure that everyone is working with the most current information.
- Access Restrictions: Limit access to sensitive documents to relevant personnel only, enhancing confidentiality and security.
"Maintaining a meticulous record of procedures ensures that knowledge is preserved within the organization, even when team members change."
Training and Competency Management
In the age of information, training should not be an afterthought; it’s the lifeblood of a competent workforce. Training and competency management hone in on ensuring that staff members possess the necessary skills and knowledge to perform their roles competently. This aspect of a QMS involves both initial onboarding and ongoing training initiatives.
Why It Matters: Proper training leads to fewer errors and heightened confidence in task execution. When employees are equipped with the right tools and knowledge, they contribute more effectively to overall operational goals.
Key Considerations for Implementation:
- Initial and Continuous Training: Make sure that training doesn’t end after the first month of employment. Regular sessions keep skills sharp and encourage adaptation to new protocols.
- Competency Assessments: Conduct routine evaluations to ascertain that team members meet the required performance standards.
Non-Conformance Management
Non-conformance management deals with the identification, documentation, and action taken when processes deviate from established norms. This aspect of QMS is crucial for maintaining integrity and quality standards within laboratory environments.
Purpose: It allows for quick rectification of issues and minimizes their potential impacts, ultimately working to identify root causes of discrepancies. Rather than treating symptoms, this approach aims at resolving the underlying problems, which could be procedural, human error-related, or even the system itself.
Steps for Effective Non-Conformance Management:
- Identification: As soon as a deviation is noticed, it should be documented to capture the specifics.
- Investigation: Don't just sweep it under the rug—analyze the issue to find its source.
- Corrective Actions: Determine a clear path to resolve the issue and prevent recurrence.
In summary, the key components of a QMS act as the pillars that support a quality-driven culture. Document control ensures transparency, training fosters competency, and non-conformance management highlights the importance of a proactive approach to quality. Each component, with its unique role, meshes seamlessly with the others, creating a robust framework that is essential for laboratories looking to not only meet but exceed quality benchmarks.
The Role of Laboratory Information Management Systems
Laboratory Information Management Systems (LIMS) play a pivotal role in enhancing the operational efficiency of laboratories. These systems are not just a fancy piece of tech; they're foundational to how modern labs function. At their core, LIMS help manage samples, associated data, and laboratory workflows. This leads to streamlined processes, better data management, and adherence to regulatory compliance, all of which are crucial for maintaining quality and effectiveness in any laboratory setting.
Streamlining Lab Processes
Efficient processes are the lifeblood of any laboratory. LIMS addresses inefficiencies that can creep in when managing specimens and experiments manually. By automating routine tasks—like sample tracking or data entry—LIMS reduces the chances of human error. For instance, a lab using a LIMS can easily log a new sample and track its status without digging through piles of paperwork or falling prey to miscommunication. This not only saves time but can also enhance the accuracy of results.
Key benefits of streamlining lab processes include:
- Faster turnaround times: Automated workflows allow labs to complete tests and analyses more quickly.
- Improved collaboration: With a centralized system, team members can access real-time data, making collaborative efforts much smoother.
- Resource optimization: Labs can gauge where resources are being allocated and adjust as necessary, leading to better overall management.
Data Management and Analysis
As data continues to grow exponentially, especially in scientific fields, managing that data effectively is more vital than ever. Here, LIMS come into play by providing robust data management capabilities. They can store vast amounts of information securely, allowing for easy retrieval and analysis. LIMS software often comes equipped with advanced analytics tools that make interpreting complex datasets a breeze.
In practice, this means a laboratory can produce reports at the click of a button—summarizing trends, anomalies, or compliance metrics. This is especially invaluable in environments focusing on research and development, where timely and accurate data analysis can lead to breakthrough findings.
Regulatory Compliance and Reporting
In the world of laboratory work, compliance isn't just a checkbox on a list; it’s an essential component of operations. Laboratories must comply with various regulations, depending on their focus area—be it pharmaceuticals, environmental testing, or others. LIMS simplifies compliance by maintaining detailed records and logs, which are essential during audits or inspections.
Furthermore, these systems facilitate automatic reporting, which not only saves time but also ensures that reports are generated consistently and accurately. An important aspect of LIMS is their ability to flag non-compliance issues before they become major problems.
"With a robust LIMS, compliance isn't just easier—it's a built-in feature that can safeguard your lab's reputation and credibility."
The End
In summary, Laboratory Information Management Systems are indispensable for modern laboratories aiming to improve operational efficiency. By streamlining processes, enhancing data management capabilities, and simplifying regulatory compliance, LIMS provide the infrastructure needed for labs to thrive in a complex and fast-paced environment. For small to medium-sized businesses and entrepreneurs in the market, adopting a LIMS can be a game-changer, leading to more precise outcomes and ultimately boosting overall performance in a competitive space.
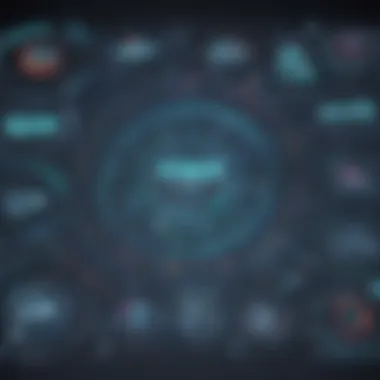
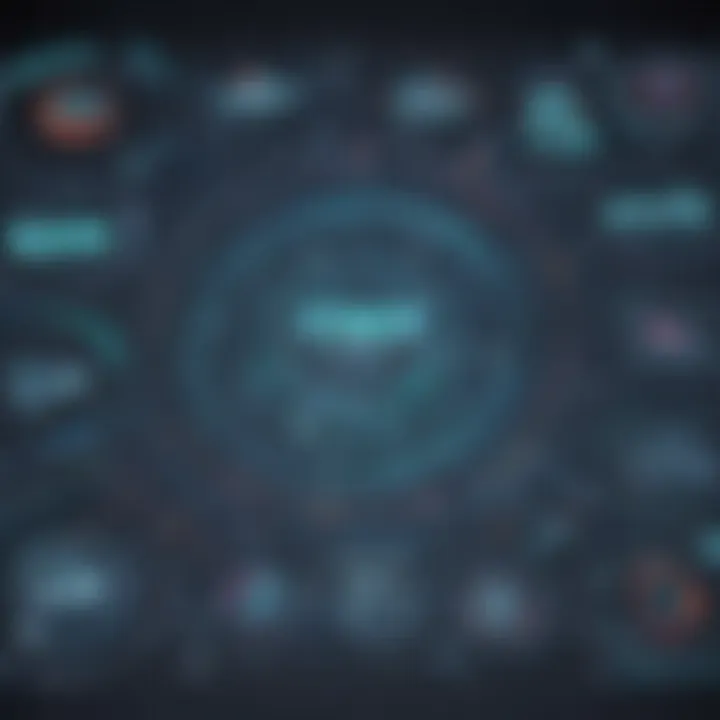
Integration between QMS and LIMS
Integrating Quality Management Systems (QMS) with Laboratory Information Management Systems (LIMS) is not just a nice-to-have; it’s a necessity for organizations aiming to maximize their operational effectiveness. As laboratories today face increasing demands for efficiency, quality, and compliance, the joining of these two systems emerges as a powerful strategy. This integration addresses core challenges such as data consistency, regulatory adherence, and streamlined workflows. When executed well, the synthesis of QMS and LIMS can serve as a backbone that supports not only day-to-day operations but also long-term organizational goals.
Benefits of Integration
The benefits that arise from integrating QMS with LIMS are manifold. Here are some key aspects worth noting:
- Enhanced Data Consistency: When QMS and LIMS are integrated, data entry is drastically reduced. This leads to fewer discrepancies and better data quality, as information only needs to be entered once. Consequently, this helps in maintaining uniformity in reports, which is vital for regulatory compliance.
- Improved Workflow Efficiency: By connecting these systems, laboratories can automate workflows. This means that tasks such as sample tracking and documentation occur seamlessly, freeing up staff to focus on more critical tasks. Think of it as moving from pedals to a power boost in an already efficient engine.
- Increased Regulatory Compliance: Regulatory bodies require organizations to adhere to strict guidelines. An integrated system not only simplifies compliance tracking but also streamlines the process of generating reports. This compliance can be effortlessly maintained and easily demonstrated during audits.
- Better Resource Management: Integrating QMS and LIMS enables businesses to better allocate resources. Real-time data provides insights on resource utilization, allowing managers to make informed decisions whether it’s about personnel or materials.
"The synergy between QMS and LIMS not only excels operational frontiers but fundamentally shifts how organizations manage quality and compliance in an increasingly intricate landscape."
- Cost Savings: Over time, reduced errors and improved efficiency lead to significant cost savings. Labor costs diminish as processes are automated, and administrative burdens are lessened.
Challenges in Integration
While the integration of QMS and LIMS offers lucrative benefits, it isn't without its challenges. Organizations must be vigilant and plan for potential roadblocks:
- Complexity of Implementation: Merging these systems can be quite complex. Each organization has unique needs, and off-the-shelf solutions might require customization. This can require rigorous planning and skilled manpower, which might strain initial budgets.
- Data Migration Issues: Transferring data from one system to another can present risks, especially if data formats do not align. Without a proper strategy, it’s easy for crucial information to get lost in the shuffle, leading to operational setbacks.
- User Resistance: Employees accustomed to existing workflows may resist changing to a new integrated system. Effective training and change management initiatives are essential to minimize pushback from staff who may view change as additional work.
- Ongoing Maintenance Needs: Integration isn't a one-time task; it requires continuous upkeep. This can lead to ongoing costs and resource allocation issues over time. Organizations must factor in these needs to avoid future headaches.
Impact on Operational Efficiency
Operational efficiency stands at the crossroads of Quality Management Systems (QMS) and Laboratory Information Management Systems (LIMS). With both systems designed to drive excellence, understanding their impact can set the stage for success or failure in laboratory environments. The harmony between QMS and LIMS doesn’t just ease operational hurdles; it shapes the landscape of productivity and resource utilization.
Let’s take a closer look at specific elements that underscore the importance of operational efficiency in this context.
Reducing Errors and Enhancing Accuracy
One of the striking features of integrating QMS with LIMS is their combined ability to minimize errors. Managing errors in a lab setting is like trying to keep a boat from leaking—you must be vigilant. By employing a robust quality management framework, labs can streamline processes that typically allow for human error, such as data entry and sample tracking.
Consider a scenario in a clinical research lab dealing with multiple samples daily. The integration of LIMS seamlessly tracks samples from collection to analysis. If a sample is misidentified, it can lead to faulty results, compromising research quality. Here, the QMS will facilitate systematic checks, ensuring every step meets precise standards.
Additionally, let's not forget about training. A strong QMS encompasses training programs focused on best practices, boosting the workforce's competency. Without it, even the best LIMS can fail to deliver desired outcomes.
"Reducing errors is not just about systems; it’s about cultivating a culture of quality that permeates every level of operation."
Optimizing Resource Management
Resource management often feels like juggling flaming torches while blindfolded. However, with a well-integrated QMS and LIMS, this becomes significantly less daunting. These systems work together to optimize laboratory resources—be it manpower, equipment, or time.
For instance, using data analytics from LIMS can shed light on usage patterns of equipment and reagents. When paired with QMS, this data can feed back into the decision-making process to enhance procurement strategies or optimize scheduling, minimizing downtime. Instead of buying in bulk and risking waste, labs can adapt to real-time demands.
Some key areas of focus include:
- Inventory Control: Track supplies accurately, preventing stockouts or overstock situations.
- Scheduling: Utilize available capacity efficiently, ensuring that each piece of equipment is in use as much as possible.
- Budget Management: Analyze operational costs and identify areas for savings without compromising quality.
Balancing all these elements results in a smoother operation, illustrated by fewer hiccups and better response times to workload changes. This not only contributes to the internal workings but also enhances client trust in the lab’s service reliability.
Considerations for Choosing QMS and LIMS
When small to medium-sized businesses think about implementing Quality Management Systems (QMS) and Laboratory Information Management Systems (LIMS), there are several key aspects to weigh. These decisions often shape not just compliance capabilities but overall operational effectiveness in laboratory settings. Understanding the specific needs of your organization lays the foundation for choosing the right systems.
Scalability and Customization
Scalability is a crucial factor when selecting QMS and LIMS. As businesses grow, their needs evolve, and the systems put in place should accommodate these changes without a hitch. Imagine a small lab that expands its operations. If the chosen LIMS cannot manage more data or users, the whole operation might grind to a halt. Therefore, ensuring that these systems can scale to meet future demands is vital to avoid disruptions down the line.
Customization is equally important. The lab environment isn't one-size-fits-all; different fields require unique functionalities. For instance, a pharmaceutical lab will have different data pathways compared to an environmental lab. Opting for systems that offer flexibility allows businesses to tweak processes, incorporate new compliance requirements, and ensure effective workflows.
In assessing scalability and customization, ask potential vendors about their track record with growth. Look for these characteristics:
- Flexibility: Can the system accommodate unique workflows?
- Integration: Does it connect easily with other tools already in use?
- User Experience: Is it intuitive for all staff levels?
By ensuring your systems can adapt, you not only safeguard your investment but also enhance productivity over time.
Vendor Support and Training
Vendor support emerges as another critical avenue that organizations must not overlook. Effective maintenance and assistance can bridge gaps on tough days when the systems might face hiccups. A dependable vendor will not only provide immediate support but will also engage in your ongoing training needs.
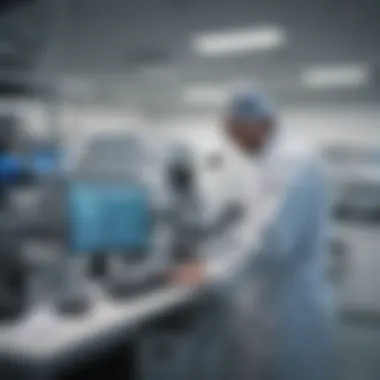
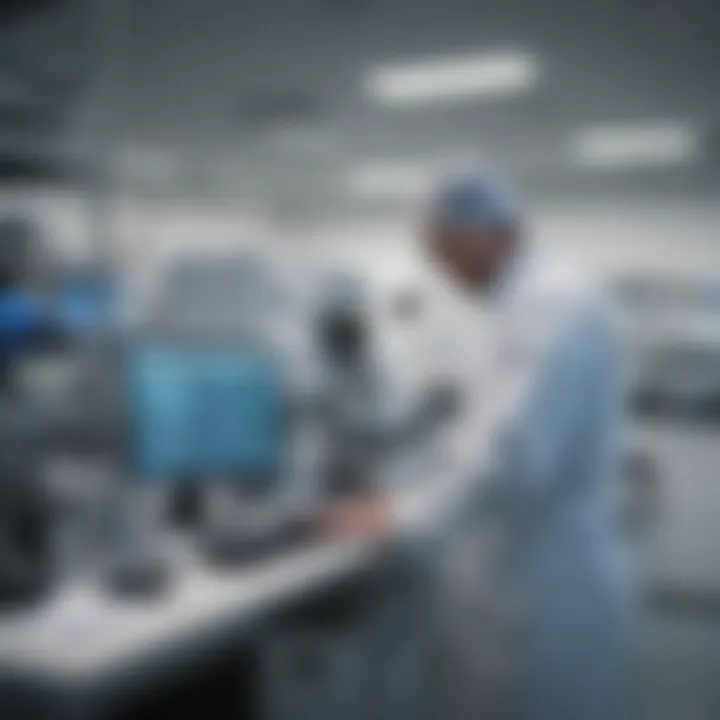
Training programs should address both technical and user-friendly aspects, enabling every employee to utilize the system to its full extent. If staff can navigate the functionalities well, it drives faster adoption and minimizes errors. Review these points when considering vendor support:
- Timeliness: How responsive is the vendor during issues?
- Training resources: Are there comprehensive materials available such as webinars or manuals?
- Community: Is there an active support forum for user interaction?
"Choosing the right vendor includes looking beyond just initial sales support; ongoing relationships matter significantly too."
Deciding on QMS and LIMS is a significant undertaking and deserves meticulous consideration. Factors like scalability, customization, and robust vendor support can set the stage for lasting operational successes.
Future Trends in QMS and LIMS
The landscape of Quality Management Systems (QMS) and Laboratory Information Management Systems (LIMS) is continuously evolving. Keeping an eye on future trends is crucial for organizations looking to refine their processes, ensure compliance, and stay ahead in a competitive market. The increasing complexity of data, alongside regulatory demands, necessitates agile adaptations in these systems. Here, we will examine two pivotal trends: the adoption of AI and automation, and the rise of cloud-based solutions. These shifts are not just about technology; they signify a strategic move toward achieving greater operational efficiency and enhanced decision-making.
Adoption of AI and Automation
AI’s role in QMS and LIMS is not merely a buzzword; it’s shaping how laboratories operate. Integrating AI capabilities allows systems to analyze data more effectively, offering predictive insights that can address quality issues before they escalate into problems. This proactive approach is not just beneficial but necessary in today's fast-paced environments, where the cost of errors can be staggering.
- Improved Decision-Making: AI algorithms can process vast amounts of data at lightning speed, presenting insights that assist in making informed decisions quickly.
- Efficiency Gains: Automation of routine tasks—like data entry or compliance checks—frees up valuable personnel for higher-level strategic roles. This shift enhances productivity.
- Predictive Maintenance: AI can help forecast when equipment may require maintenance. Instead of waiting for breakdowns, labs can ensure continuous operation, significantly reducing downtimes.
"As AI continues to evolve, we must consider not just what can be done, but what should be done in our systems."
All these advantages mean organizations can better assure their compliance with industry regulations while simultaneously pushing efficiency to new heights. However, the implementation isn’t without its challenges. Organizations should perform a thorough assessment of how AI tools integrate with existing systems and whether staff requires training to maximize the benefits.
Cloud-Based Solutions
As cloud technology becomes increasingly mainstream, its advantages for QMS and LIMS cannot be overlooked. Moving systems to the cloud offers numerous benefits:
- Accessibility: Stakeholders can access data remotely, fostering collaboration across various locations. This means scientists, management, and quality assurance teams can share insights seamlessly, regardless of their physical location.
- Scalability: Cloud solutions can grow with the organization. Whether it’s increasing data storage or adding new functionalities, businesses can adapt their systems without overhauling existing infrastructure.
- Cost-Effectiveness: By eliminating the need for extensive on-premises hardware, businesses can reduce upfront investments and adapt expenses based on usage. Subscription-based models often lower financial barriers for small to medium-sized enterprises.
Though cloud solutions present many advantages, organizations must consider factors like data security and compliance with regulatory guidelines. Ensuring that cloud providers adhere to industry standards can safeguard sensitive information while maintaining trust with stakeholders.
In summary, keeping an eye on these trends is vital for any organization aiming to enhance its QMS and LIMS. The combination of AI and cloud technology positions businesses to thrive in increasingly complex and regulated environments.
Case Studies: Success Stories
The relevance of case studies shines a light on the practical application of Quality Management Systems (QMS) and Laboratory Information Management Systems (LIMS). They act as a compass, guiding businesses through the intricacies of implementation while showcasing tangible benefits. Real-world examples provide invaluable insights, making abstract concepts more relatable and providing a framework for small to medium-sized businesses to assess their own strategies.
When considering QMS and LIMS, looking at success stories allows organizations to understand the road bumps encountered and how others navigated them. It emphasizes the importance of adapting these systems to the specific needs of a laboratory or a company, ensuring that they aren't just cookie-cutter solutions but rather tailored frameworks that bring about efficiency and compliance.
Pharmaceutical Industry Example
One striking example is found in the pharmaceutical sector, particularly with a major player like Pfizer. They embraced the integration of QMS and LIMS to bolster their drug development processes. This transition involved constructing a bridge between quality protocols and data management, reaping numerous benefits in the process.
- Streamlining Processes: By linking LIMS with their QMS, Pfizer minimized redundancies. Elements like documentation control and adherence to Good Manufacturing Practices became seamlessly interwoven within their lab operations.
- Data Integrity: Trust in data is key in pharmaceuticals. Pfizer saw significant improvements in data accuracy. With a well-integrated system, they could easily trace data back to its origin, ensuring compliance with regulatory bodies such as the FDA.
- Faster Decision-Making: The real-time access to data allowed for quicker cross-functional decisions, speeding up product releases.
This case exemplifies the impact effective systems can have not only on workflow but also on compliance and product integrity. Other companies looking to boost their operational capabilities can draw lessons from Pfizer's execution and adaptability.
Environmental Labs
On the flip side, environmental labs also provide a noteworthy context to explore the interplay of QMS and LIMS, particularly through examples like the Environmental Protection Agency (EPA). Here, the focus is on research and compliance, vital for validating environmental monitoring programs.
- Quality Assurance: One of the key focuses was improving data reliability for environmental assessments. The EPA adopted robust QMS practices to ensure that data from various locations maintained integrity.
- Efficiency in Reporting: Integration with LIMS allowed for the automatic generation of reports, saving countless hours of manual labor, which is crucial in an industry where timing can mean preventing environmental disasters.
- Collaboration and Training: The success was not only in technology but also in investing in training for staff, fostering a skilled workforce adept at using the systems.
These cases remind business professionals that both sectors, though vastly different, share common ground when it comes to enhancing operational efficiency through thoughtful application of quality systems.
"Learn from the successes of others by examining case studies. They can illuminate the path and provide a roadmap for your own journey."
By diving into these real-life examples, those in the field can not only appreciate the strengths of QMS and LIMS but also begin crafting their own narratives of success.
Closure: The Importance of QMS and LIMS
In today’s fast-paced and ever-changing business landscape, the synergy between Quality Management Systems (QMS) and Laboratory Information Management Systems (LIMS) plays a pivotal role. These systems are not merely optional; they serve as foundational elements that enhance operational efficiencies, foster compliance, and drive data integrity in laboratories. When companies recognize the significance of these systems, they unlock a pathway to sustained growth and competitive advantage.
Summarizing Their Value
The integration of QMS and LIMS brings several benefits that cannot be overlooked.
- Consistency and Accuracy: Together, these systems ensure that every process is meticulously followed, thus minimizing errors. In laboratory settings, even small mistakes can lead to significant issues. By employing QMS alongside LIMS, you maintain high standards consistently.
- Enhanced Data Integrity: With LIMS managing data and QMS regulating processes, there’s a robust mechanism for preventing data loss or corruption. Ensuring complete and accurate data is key for regulatory compliance, which can’t be taken lightly in industries such as pharmaceuticals or environmental testing.
- Customer Confidence: When the systems work hand in hand, it fosters trust from clients. They’re assured that the quality of work performed meets or exceeds standards, thus enhancing overall satisfaction.
"Quality is never an accident; it is always the result of intelligent effort." - John Ruskin
This quote underscores the essence of having a well-integrated QMS and LIMS.
Future Directions for Businesses
As we look toward the future, there are several considerations businesses should keep in mind.
- Embracing New Technologies: Integrating AI and machine learning with QMS and LIMS could offer never-seen-before efficiencies. Analyzing large datasets becomes easier, and predictive analytics can forewarn about potential issues.
- Greater Cloud Adoption: The shift to cloud-based solutions offers real-time accessibility and collaboration. This means multiple stakeholders can engage with the data without compromising security or quality.
- Increasing Customization: As individual laboratory needs vary widely, custom solutions will become more critical. Look for flexible providers that allow customization tailored to specific workflows.
With these elements in view, small to medium-sized businesses, as well as entrepreneurs and IT professionals, must stay alert to the evolving landscape. The interplay of QMS and LIMS should not be neglected; rather, it’s an investment in the future that promises a resilient operational framework and heightened regulatory compliance.