A Deep Dive into Logiwa WMS Software Solutions
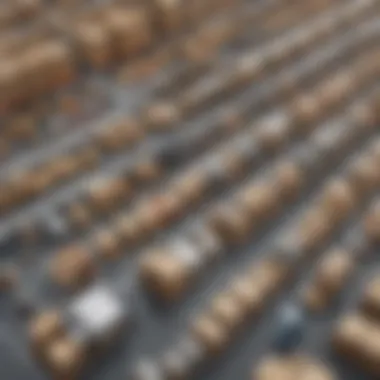
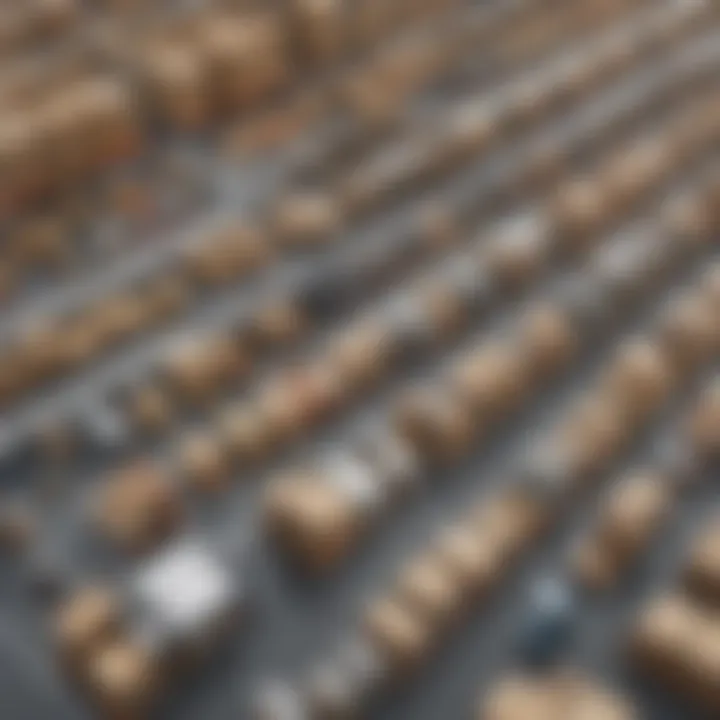
Intro
In the ever-evolving world of logistics and supply chain management, having the right tools can make or break a business. Logiwa WMS software emerges as a vital player in this landscape. Designed specifically for warehouse management, it aims to optimize operations for businesses of all sizes. Whether you're a small entrepreneur starting your journey or a seasoned IT professional managing complex systems, understanding how this software operates is crucial.
One of the key advantages of Logiwa is its user-friendly interface. It streamlines processes, simplifying tasks that can often overwhelm even the most organized managers. This guide will take you through the essential features, benefits, potential drawbacks, and the implementation process, helping you navigate through the ins and outs of Logiwa WMS software.
More than just a list of capabilities, this exploration seeks to provide substantial insights into how Logiwa stands apart from its competitors. As we delve deeper, we’ll spotlight its core functionalities, the challenges it may present, and the strategic advantages it can furnish—ultimately aiming to equip you with the knowledge necessary for informed decision-making in your warehouse management endeavors.
Preamble to Warehouse Management Systems
In today’s fast-paced business world, effective warehouse management plays a crucial role in ensuring operational efficiency. Knowing how to manage inventory, streamline processes, and maximize space can mean the difference between a thriving business and one that struggles to keep up. In this section, we’ll delve into the essence of Warehouse Management Systems (WMS) and outline their significance in the grand scheme of logistics and supply chain management.
Understanding Warehouse Management
Warehouse management is a vital component of supply chain operations. It encompasses a variety of activities, from managing inventory levels to overseeing the movement of goods in and out of a warehouse. Without proper management, a warehouse can quickly become a chaotic space, leading to misplaced products, slow order fulfillment, and ultimately dissatisfied customers.
What’s key here is not just the physical organization of goods, but also the strategic planning involved in optimizing storage space, improving picking and packing accuracy, and ensuring timely deliveries. In essence, a well-managed warehouse acts like the engine of a well-oiled machine—when all components work in harmony, efficiency skyrockets.
The Role of Software in Warehouse Efficiency
Here’s where warehouse management software comes into play. Imagine trying to navigate a busy intersection without traffic signals—utter pandemonium. Similarly, software solutions like Logiwa WMS provide the necessary framework to keep warehouse activities organized and efficient.
With features like real-time inventory tracking, many businesses can manage their stock levels more accurately. This software helps in:
- Reducing human errors in inventory counts
- Streamlining order picking processes
- Facilitating efficient space utilization
- Enhancing transparency in operations
As a result, businesses not only save time but also significantly cut costs. In other words, adopting a robust WMS is akin to installing GPS in your delivery vehicles—suddenly, everything becomes clearer and you can make informed decisions based on accurate data.
"In today's competitive marketplace, efficient warehouse management using the right software is not just an advantage; it's a necessity."
This overview of warehouse management sets the stage for a deeper exploration into Logiwa WMS—its features, benefits, and what businesses can expect from implementing such a solution.
What is Logiwa WMS Software?
Logiwa WMS Software stands as a pivotal player in the realm of warehouse management. By harnessing the power of modern technology, it not only streamlines operations but also optimizes overall efficiency. For businesses looking to improve their supply chain workflow, understanding Logiwa's specific functionalities is essential. The software provides tools that address a wide array of logistical challenges. This article aims to dissect these components, offering insights for entrepreneurs, IT professionals, and small to medium-sized businesses alike.
Overview and Origin of Logiwa
Logiwa originated from the need for more effective solutions in warehouse management. Founded with a vision to simplify complex logistical operations, it has quickly become a reliable choice for companies of various sizes. This software was designed to address the growth of e-commerce and the shifting landscape of inventory management.
The platform emerged as a result of extensive research into the challenges faced by warehouses. Whether dealing with seasonal surges or consistently high throughput, Logiwa provides versatile tools that adapt to each unique situation. Moreover, its user-friendly interface speaks to a commitment towards making warehouse operations smoother and more efficient. Logiwa's foundation is not just a product of technological advancements but also rooted in understanding what businesses truly need.
Core Objectives of Logiwa WMS
The core objectives of Logiwa WMS revolve around enhancing efficiency, accuracy, and responsiveness in warehouse operations. Here are the primary goals:
- Streamlining Operations: At the heart of Logiwa's design is the goal to eliminate inefficiencies that can slow down processes. Keeping tasks connected and reducing redundancy helps improve overall productivity.
- Providing Real-time Visibility: Logiwa emphasizes transparency through real-time inventory tracking. This ensures that managers can always maintain control, regardless of warehouse size.
- Facilitating Decision Making: With integrated analytics, Logiwa enables data-driven decisions. This aligns operational tasks with business goals and objectives, making it a vital tool for strategic planning.
- Enhancing Customer Satisfaction: By enabling faster order fulfillment and accuracy, Logiwa directly impacts customer satisfaction, which is a crucial aspect for businesses today.
In summary, Logiwa WMS Software serves as a bridge between the complexities of logistics and the simplicities of effective management. It invites businesses to rethink how they handle warehousing and inventory, paving the way for future growth and success.
"The future of logistics is not just about transporting goods; it's about creating a seamless experience for every stakeholder involved."
Through a comprehensive understanding of Logiwa WMS, businesses can better adapt to the ever-changing demands of the market.
Key Features of Logiwa WMS
When discussing warehouse management systems, it's imperative to consider the specific features that enable these tools to maximize efficiency and effectiveness. Logiwa WMS stands out because its design focuses not only on operational fluency but also on adaptable solutions for diverse business needs. Below, we delve deep into the features that give Logiwa its edge, as well as their implications on everyday usage.
Inventory Management
Real-time Inventory Tracking
Real-time inventory tracking is one of the hallmarks of Logiwa WMS. It allows businesses to monitor stock levels continuously, ensuring that they have the right products available without overstocking. The key characteristic here is immediacy; with real-time updates, businesses can respond swiftly to customer demands. This immediacy is an essential factor for any thriving business, as it reduces instances of stockouts and enhances responsiveness.
The unique feature of this tracking system is its integration with barcoding and RFID technology. This means that as items move in and out of the warehouse, their statuses are updated instantly. However, while this feature boasts many advantages, like reducing miscounts and improving order accuracy, it also requires a solid internet connection and reliable devices to scan items effectively.
Stock Level Management
Stock level management plays a critical role in the operational success of any warehouse. Logiwa’s system notifies managers when stock hits certain thresholds, which effectively prevents both surpluses and shortages. By maintaining equilibrium, businesses can align their storage costs more closely with their purchasing patterns.
The standout aspect of stock level management in Logiwa WMS is its predictive analytics capability. By analyzing sales trends, it forecasts future needs, enabling businesses to make informed stocking decisions. This can be a game changer for firms operating under tight margins. It’s worth mentioning, however, that relying solely on predictive analytics can sometimes lead to overestimating demand, particularly if market conditions shift unexpectedly.
Order Fulfillment
Picking and Packing
Picking and packing processes are vital to order fulfillment in any warehouse operation, focusing heavily on accuracy and speed. Logiwa excels in this aspect by providing a streamlined method that guides team members through the steps needed to prepare an order.
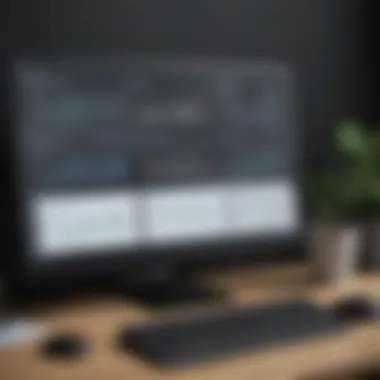
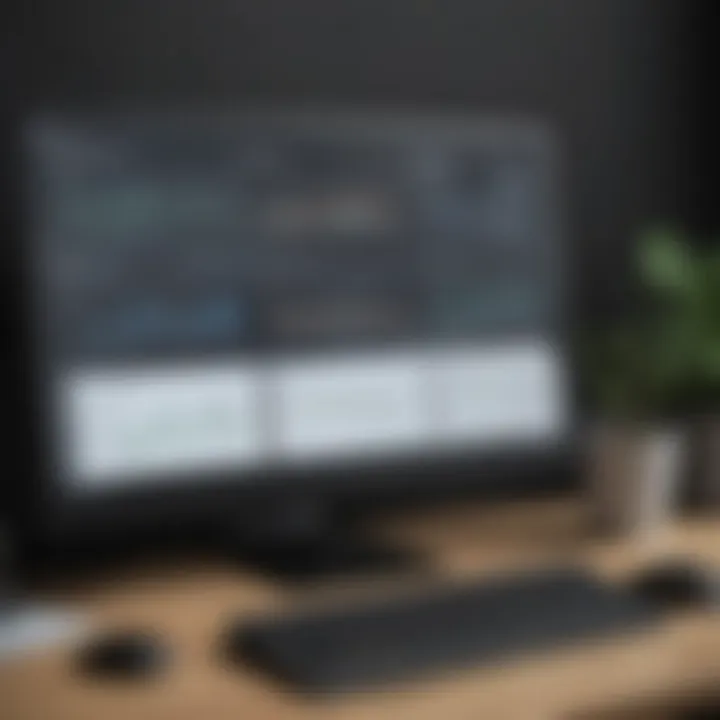
The highlight of Logiwa’s picking and packing feature is the intuitive user interface. Workers can easily access information about order priorities and item locations. This efficiency often results in shorter turnaround times, essential for e-commerce businesses aiming for quick shipping. However, during peak seasons, even the best systems may encounter bottlenecks, requiring a supplementary workforce.
Shipping Integration
Shipping integration is the backbone connecting inventory management to customer satisfaction. Logiwa WMS makes it easy to connect with multiple shipping carriers, delivering flexibility in choosing the best options for each order. This functionality enables businesses to provide more shipping alternatives, an important factor for customer loyalty.
The unique aspect of this integration is how it automates shipping label creation and tracking updates. These features markedly enhance user experience by reducing manual entry errors and providing customers with timely updates. Still, integrating with multiple carriers can sometimes lead to complexities in managing rates and service levels, requiring constant vigilance from warehouse managers.
Reporting and Analytics
Performance Metrics
Performance metrics are critical for evaluating operational efficiency within a warehouse. Logiwa provides a robust tool that enables users to gauge their fulfillment and inventory processes systematically. The key characteristic of these metrics is their ability to pinpoint areas for improvement, thus allowing businesses to allocate resources more efficiently.
One unique feature of Logiwa's reporting is its ability to generate customizable dashboards that reflect real-time data. This visibility allows managers to see what’s happening at a glance. However, businesses need to ensure they follow up on the insights from these metrics; neglecting them would harbor missed opportunities for improvement.
Data-Driven Insights
Data-driven insights are what separate the leaders from the laggards in warehouse management. Logiwa WMS collects vast amounts of data that can inform strategic decisions. These insights enhance the understanding of market trends and consumer behavior, contributing to long-term growth.
What makes this feature powerful is its algorithmic analysis that identifies underlying patterns in data. Companies can adjust their strategies based on these insights, thereby streamlining their operations more effectively. The downside is that businesses may find themselves overwhelmed by data, necessitating proper training on how to interpret and act on these insights effectively.
Benefits of Implementing Logiwa WMS
Implementing Logiwa WMS is not merely a technological upgrade; it represents a strategic move that brings significant advantages to businesses of all sizes. This software accommodates the complexities of today’s supply chains and addresses the specific challenges faced by warehouse management. By adopting this system, businesses can experience numerous efficiencies that contribute directly to their bottom line. Let's delve into the key benefits.
Cost Efficiency
In the world of business, the bottom line often determines the survival of a company. Logiwa WMS offers substantial cost benefits that can improve profit margins. With its robust inventory management tools, companies can allocate resources more wisely, eliminating surplus or unnecessary stock that ties up capital.
Moreover, the automation of many warehouse processes leads to reductions in labor costs. When order fulfillment is streamlined, fewer workers are needed to complete tasks, and those employees can focus on higher-value activities instead. Businesses can also save on storage costs by effectively managing their inventory levels, reducing the need for extra warehouse space.
Key points regarding cost efficiency:
- Reduction in labor costs due to automation
- Decreased inventory holding costs
- Better resource allocation and reduced waste
Enhanced Accuracy
In an industry where one misplaced item can lead to delays and dissatisfied customers, enhanced accuracy is a critical advantage that Logiwa WMS offers. The software minimizes human error through its integrated scanning and tracking capabilities.
With real-time tracking, companies can keep their inventory counts precise, ensuring that items are readily available when required. This accuracy extends to order fulfillment as well; shipping the right products to customers significantly enhances reliability, garnering trust in a volatile market.
Aspect of enhanced accuracy:
- Reduction of order errors and returns
- Improved inventory visibility and management
- Strengthened customer trust through reliable order fulfillment
“One error can undo months of good service,” says a warehouse manager. Invest in accuracy, and you’ll see the dividends pay off.
Improved Customer Satisfaction
Customers are the beating heart of any business, and their satisfaction is paramount. Logiwa WMS contributes extensively to customer satisfaction by ensuring that orders are processed accurately and in a timely fashion.
When customers receive their orders without delays or discrepancies, they are more likely to return. A seamless return process, empowered by WMS, can also turn a potentially negative experience into a positive one. When returns are made simple and hassle-free, customer loyalty often increases as consumers appreciate the ease of doing business.
Strategies for an improved customer experience:
- Timely order fulfillment leads to repeat customers
- Streamlined returns process strengthens customer loyalty
- Transparency and communication through real-time updates
Adopting Logiwa WMS isn’t just about technology; it's about forging better relationships with customers through reliability and excellence in service.
Together, these benefits show that the investment in Logiwa WMS is an investment in a company’s future, fostering environments where efficiency, accuracy, and customer satisfaction flourish.
Potential Drawbacks of Logiwa WMS
While Logiwa WMS software holds promise for enhancing warehouse management, it's not a silver bullet that resolves every issue a business may encounter. A thorough understanding of its potential drawbacks is crucial for small to medium-sized businesses considering this solution. Being aware of the limitations can help in setting realistic expectations and preparing adequately for a successful implementation. Let's discuss two main points: the learning curve for users and integration challenges.
Learning Curve for Users
One significant barrier for businesses adopting Logiwa WMS is the learning curve associated with its use. For employees accustomed to their existing systems, picking up a new piece of software can feel like a game of chess—one wrong move, and they might find themselves in a bind. Here's the rundown of how this learning curve can affect operations:
- Adaptation Time: Staff may require several weeks or even months to feel comfortable navigating the software efficiently. During this time, productivity might dip as users grapple with new processes.
- Training Programs: Organizations will need to invest in comprehensive training sessions. While Logiwa offers resources, the effectiveness of training vastly varies among users. Some may grasp concepts quickly, while others might struggle.
- User Resistance: There can be an inherent reluctance among employees to shift from familiar practices. This reluctance can lead to pushback during the transition—it's often more about comfort than capability.
To mitigate these issues, organizations can implement step-by-step training sessions that clear up complexity while customizing the learning process based on individual skill levels.
Integration Challenges
Another hurdle that can pop up when implementing Logiwa WMS is the challenge of integrating it with existing systems. A smooth blend of various software solutions is integral for operational efficiency, but the reality can be quite different:
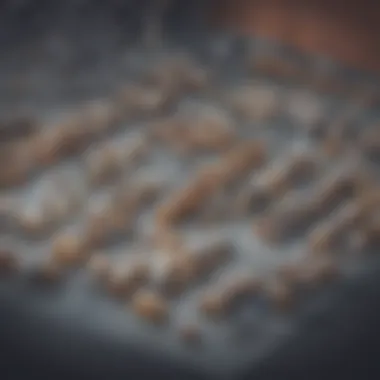
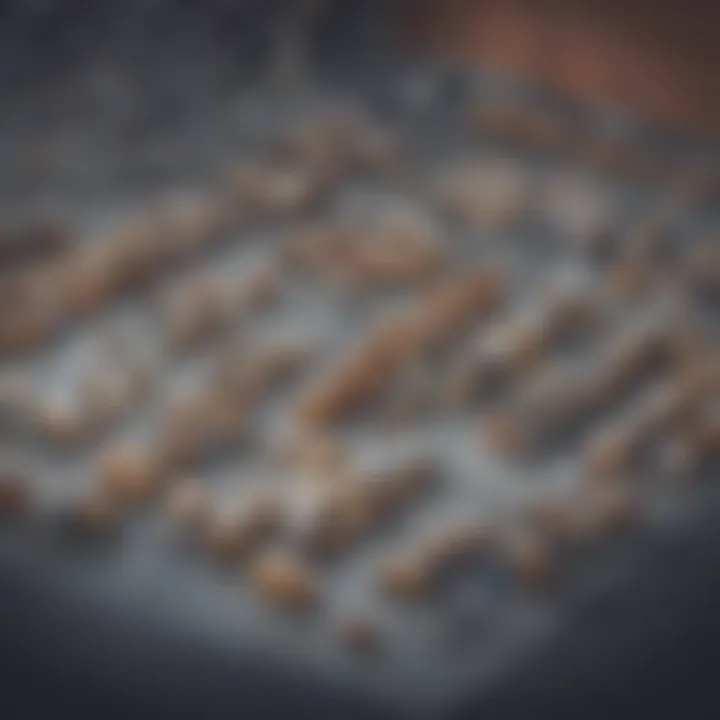
- Compatibility Issues: Not all legacy systems play nice with modern software like Logiwa. Differences in data structures and communication protocols can create roadblocks during integration.
- Data Migration: Transferring existing data to the Logiwa platform isn't always risk-free. Errors in data migration can lead to inaccuracies, impacting inventory management and reporting.
- Time-Consuming Process: The integration process can extend timelines and inflate costs. Businesses might find themselves investing more resources than anticipated to ensure that all systems work well together.
In overcoming these challenges, it's recommended to engage IT professionals who specialize in system integration. This expertise can prove invaluable in creating a fluid transition, allowing businesses to capitalize on the software’s benefits without enduring unnecessary strain.
"Understanding the potential drawbacks of any software solution is as essential as knowing its benefits; it allows for informed decision-making and smoother transitions."
Implementation Process for Logiwa WMS
The implementation of Logiwa WMS is a critical phase that directly impacts its effectiveness in enhancing warehouse operations. It’s not something to gloss over; this process paves the way for smooth sailing in daily tasks of inventory management, order fulfillment, and more. By ensuring that the new system integrates seamlessly with existing practices, businesses can maximize their return on investment and gain a competitive edge in the market.
Initial Assessment and Planning
Before jumping into the implementation, it's paramount to conduct an initial assessment. This assessment acts as a compass, guiding the project towards its overall goals. It involves evaluating current processes, identifying specific pain points, and understanding how Logiwa can address those challenges.
Key steps to consider include:
- Stakeholder Involvement: Gather insights from all involved parties, particularly those who will work directly with the WMS. Their feedback is invaluable.
- Goal Definition: Clearly outline what the business hopes to achieve with the implementation, such as reduced order processing times or improved inventory accuracy.
- Resource Allocation: Assess the budget, technology, and human resources needed for a successful rollout.
Taking time for this foundational stage can prevent stumbling blocks later on. As the adage goes, "a stitch in time saves nine." Without proper planning, the likelihood ramps up for confusion and setbacks during the actual implementation phase.
Data Migration
Once a solid plan is forged, the next hurdle is data migration. Transfering existing data into Logiwa WMS needs to be done with meticulous attention. Issues in this phase can lead to severe disruptions down the line.
The data migration process entails several critical tasks:
- Data Audit: Examine the current data to identify outdated, duplicate, or irrelevant entries. Clean datasets ensure clarity.
- Mapping Data: Determine how existing data fits into the Logiwa framework, ensuring alignment in categories, metrics, and formats.
- Testing Migration: Conduct a test run of the migration process to catch potential pitfalls before they materialize on a larger scale.
- Final Migration: After ensuring the test results are satisfactory, perform the final data transfer, followed by rigorous validation to confirm accuracy.
This phase is often described as a double-edged sword: it can either make the system's functionality sharper or cause unnecessary delays. Smooth data migration directly correlates to how well the WMS will serve its operational purpose.
Training and Support for Staff
After technical aspects are taken care of, the human element steps into play. No matter how advanced a software system is, it’s only as good as the people operating it. Training staff effectively is essential for utilizing Logiwa WMS to its full potential.
Training should encompass:
- Hands-On Workshops: Interactive sessions can solidify knowledge, allowing staff to experiment with the system.
- Documentation: Comprehensive guides that illustrate operations of the software can be a reference for employees, reducing reliance on continuing training.
- Ongoing Support: Establish a support system where questions can be answered as staff acclimates to the new software.
By investing time in training, businesses increase their chances of hitting the ground running post-implementation. Furthermore, well-trained employees not only feel confident in their roles but also contribute to higher morale and better job satisfaction.
"Training is not an expense; it's an investment in your team’s potential."
Integrating Logiwa WMS With Existing Systems
In today’s fast-paced supply chain landscape, the ability to integrate new software like Logiwa WMS with existing systems is not just a luxury; it’s essential for streamlined operations. Many businesses, especially small to medium-sized ones, have a patchwork of tools and systems in place. These can range from ERP solutions to various logistics and tracking software. Successfully integrating Logiwa WMS can lead to significant benefits, from improved data visibility to enhanced operational efficiency.
Integrating WMS software with your existing systems means bridging the gap between different functions. This is about more than just compatibility; it’s about creating synergy among various operations that usually do not speak the same language. Let’s delve deeper into two key aspects of this integration process: compatibility with ERP systems and the utility of APIs for workflow automation.
Compatibility with ERP Systems
Choosing Logiwa WMS comes with the added advantage that it can mesh seamlessly with many ERP systems. This compatibility is indispensable in ensuring that inventory data flows freely between departments, minimizing discrepancies and maximizing the accessibility of real-time information.
Benefits of integration with ERP systems include:
- Streamlined Data Management: Technical compatibility means fewer manual updates, which reduces human error.
- Holistic Reporting: When sales, finance, and inventory are linked, the reporting becomes more holistic, assisting with better decision-making.
- Cost Efficiency: The integration ultimately cuts down on labor costs because less time is spent on redundant data entry.
However, businesses must consider the specific attributes of their ERP systems. Some might require custom coding or third-party connectors to facilitate integration. If your team lacks expertise in this area, it might be worth consulting with specialists or planning for a small upskilling effort.
API and Workflow Automation
Implementing Logiwa WMS is a little like adding a high-performance engine to an already existing vehicle. But without the right API setup, you won’t be able to take advantage of everything this software offers. APIs allow different systems to communicate effectively, enabling seamless data transfers and workflow automation.
Key advantages of utilizing APIs include:
- Time Savings: Automated workflows reduce the need for manual interventions, permitting teams to focus on more significant tasks.
- Real-Time Updates: When stock counts change or orders are processed, APIs ensure that these updates are immediately reflected across systems.
- Flexibility: If your business evolves and needs to swap out an existing system or adopt new tools, APIs allow for easier adjustments without massive overhauls.
Integrating Logiwa WMS with your existing infrastructure will bring many advantages but requires careful planning. Suppose you already have a disparate system landscape that needs attention. In that case, it’s crucial to evaluate compatibility early on and research your API capabilities to ensure a smooth transition. As the saying goes, "a stitch in time saves nine." This rings particularly true in the context of software integration, where foresight can prevent bigger headaches down the line.
Successful integration can be a game-changer; it opens pathways to enhanced efficiency and better data utilization across the warehouse.
In summary, the integration of Logiwa WMS with your current systems holds the key to harnessing its full potential. It ensures that your warehouse operations are not just optimized but also positioned to adapt in an ever-evolving logistics environment.
Case Studies: Success Stories with Logiwa WMS
Analyzing case studies helps illuminate the transformative power of Logiwa WMS in various operational scenarios. These practical examples are essential for demonstrating how businesses leverage the software to adapt and thrive. The importance of case studies lies not only in showcasing successes but also in revealing actionable strategies that can be applied in different contexts. By diving into specific experiences of e-commerce businesses and manufacturers, we get a clear picture of just how beneficial Logiwa can be.
E-commerce Business Transformation
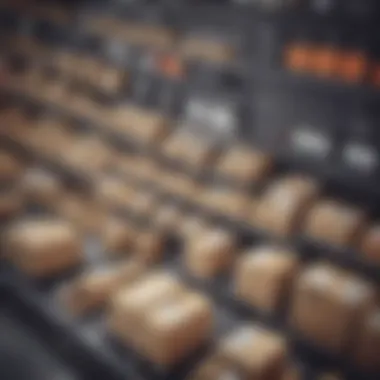
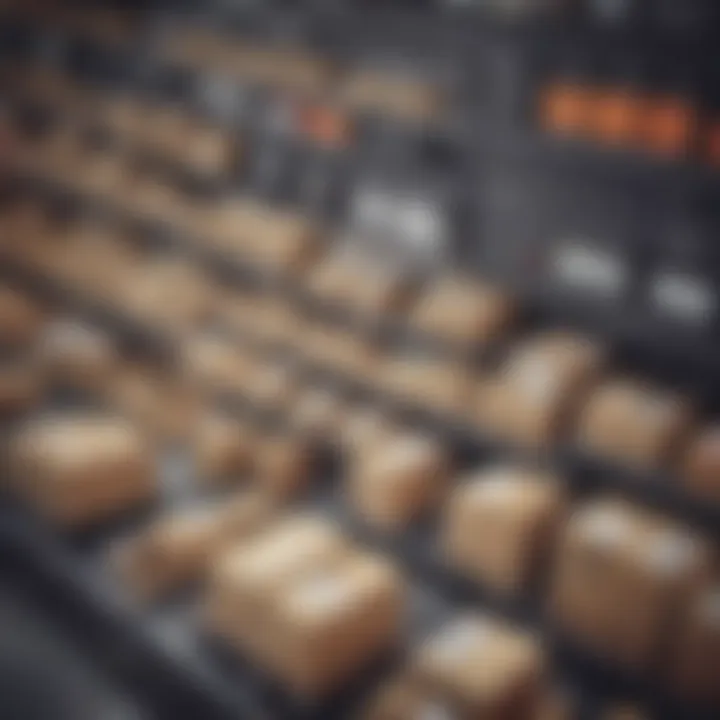
A notable example of Logiwa WMS's impact can be drawn from an e-commerce business that sells outdoor gear. Faced with fast-paced consumer demands, this company struggled to manage inventory efficiently, leading to stockouts and frustrated customers.
By implementing Logiwa WMS, they were able to integrate real-time inventory tracking, which allowed them to monitor stock levels accurately. This feature not only streamlined their order fulfillment process but also improved their ability to forecast demand. The result? A staggering 40% reduction in shipping errors and a 30% increase in overall customer satisfaction ratings. Customers began to trust the business more, knowing their orders would arrive correctly and swiftly.
From this story, we can glean that the real-time inventory features are crucial for e-commerce operations. They not only enhance operational efficiency but also significantly impact customer loyalty. Companies in similar industries can consider investing in similar technologies to avoid falling behind.
Manufacturing Process Optimization
Shifting focus, let’s examine a mid-sized manufacturer specializing in automotive parts production. The company was plagued by inefficient workflows and communication breakdowns among its inventory and production teams. This led to delays that ultimately hurt their bottom line.
After introducing Logiwa WMS, the manufacturer saw a remarkable transformation in its operations. It adopted the software's API and workflow automation capabilities, enabling seamless communication between various systems including its Enterprise Resource Planning (ERP) setup. This integration streamlined the inventory process, reducing errors associated with manual data entry. The results were eye-opening: a 25% increase in production efficiency and a remarkable 20% decrease in lead times.
Furthermore, the data-driven insights generated through Logiwa's reporting functions enabled the team to identify bottlenecks and make informed decisions. The manufacturer actively used these insights to optimize resource allocation and improve overall workflow. This case underscores the importance of not just implementing software, but using it strategically to drive performance.
Ending
These case studies clearly illustrate the capabilities of Logiwa WMS in tackling real-world business challenges. Whether it’s an e-commerce outfit needing to fulfill orders more accurately or a manufacturer seeking to enhance production efficiency, the lessons learned from these examples can inform other businesses looking to navigate their own operational hurdles with similar tools. In today’s competitive market, understanding such transformations can help decision-makers avoid costly mistakes and inspire innovative solutions.
Alternatives to Logiwa WMS
In an ever-evolving landscape of warehouse management systems, exploring alternatives to Logiwa WMS holds significance. Businesses might not find Logiwa to align perfectly with their operational goals, technical requirements, or budget constraints. Therefore, developing an understanding of available alternatives can guide decision-making, ensuring a match between software capabilities and business needs.
When considering alternatives, it's essential to evaluate what features and benefits each option brings to the table, alongside the specific challenges faced in your warehouse operations. Here are a few factors to think about:
- Scalability: Can the software grow with your business?
- Integration: How well does it connect with your existing systems?
- User-Friendliness: Is the interface intuitive enough for your team?
- Customer Support: What kind of support is available post-implementation?
Comparing Popular Warehouse Management Software
It’s not just about finding other software; it's also important to directly compare them to see how they measure up against Logiwa WMS. Here’s a breakdown of some popular contenders:
- Fishbowl Inventory: This software provides extensive inventory management features that appeal to manufacturing and e-commerce companies. With real-time tracking, businesses can maintain better control of their stock.
- Lightspeed Retail: Primarily known for its point-of-sale systems, Lightspeed has functionalities that cater well to retail operations, integrating inventory management and customer relationship features.
- NetSuite WMS: A robust option that integrates seamlessly within the ERP framework. NetSuite offers comprehensive analytics and reporting capabilities, but might come with a higher price tag.
Each of these options has its own strengths. For example, Fishbowl shines in its inventory tracking abilities, while NetSuite stands out with its integration capabilities.
Evaluating Pricing Models
Choosing a WMS isn't just about features; pricing models greatly influence your financial decisions. Here’s how you can evaluate the financial aspects effectively:
- Subscription vs. One-Time Fee: Assess whether the software operates on a subscription basis or requires a one-time payment. A subscription model may seem easier on cash flow but can accumulate costs over time.
- Hidden Costs: Always consider additional expenses such as setup fees, training costs, or charges for technical support. These can create a more accurate picture of your total cost of ownership.
- Trial Periods: Many software providers offer trials. Whether it’s a 30-day test drive or a freemium model, such options can help gauge value without a financial commitment.
By analyzing these alternatives and their pricing models, businesses can make informed choices that are well-tailored to their operational needs. As with all tech investments, due diligence is critical. The decision-making process should incorporate not just current requirements but also future growth objectives.
Future Trends in Warehouse Management Software
The landscape of warehouse management is constantly shifting, driven by technological innovations and evolving business needs. Understanding these future trends is essential for small and medium-sized businesses, entrepreneurs, and IT professionals aiming to stay competitive. Warehouse Management Software, like Logiwa WMS, plays a crucial role in helping businesses navigate these changes efficiently.
Technological Advancements
In the fast-paced realm of warehousing, technology is often the cornerstone of progress. Several technological advancements are projected to shape the future of warehouse management:
- Artificial Intelligence (AI) and Machine Learning: AI is set to revolutionize inventory management by predicting stock levels and optimizing order fulfillment processes.
- Internet of Things (IoT): Tools such as smart shelves and connected devices facilitate real-time tracking of inventory and equipment, making it easier to manage stock and reduce losses.
- Automation and Robotics: The emergence of automated guided vehicles and robotics in warehousing can streamline operations, significantly cut down labor costs, and minimize human error.
- Cloud Computing: Cloud-based WMS solutions enable seamless data sharing and real-time communication across various platforms, fostering collaboration among teams and enhancing operational efficiency.
These advancements not only boost efficiency but also pave the way for easier integration with e-commerce platforms and ERP systems. In a nutshell, harnessing the power of technology means better decision-making and a competitive edge.
Shifts in User Expectations
As customers and businesses evolve, so do the expectations of warehouse management solutions. Here are a few noteworthy shifts that are influencing user preferences:
- User Interface and Experience: A user-friendly interface is now paramount. Warehouse staff prefer intuitive designs that minimize training time and allow for quicker adaptation.
- Real-time Data Access: Users increasingly seek instant access to data for informed decision-making. Dashboards providing insights at a glance have become a must-have feature.
- Flexibility and Scalability: With many businesses facing fluctuating demands, scalable solutions allow companies to adjust their operations in response to seasonal changes without incurring high costs.
- Integration Capabilities: Users expect their warehouse management systems to seamlessly integrate with existing platforms, ensuring continuity across various operational touchpoints.
The convergence of these trends paints a vivid picture of the warehouse management future. Not only will businesses benefit from enhanced efficiencies, but they will also find themselves aligning more closely with customer demands.
"In the world of warehouse management, staying ahead means embracing change and anticipating what’s next. The capacity to adapt will determine the success of future businesses."
By staying informed of these trends, companies can position themselves not just to survive but to thrive in an ever-evolving market.
Epilogue and Recommendations
Summarizing everything concerning Logiwa WMS, it’s palpable that this software serves as a crucial player in the ever-evolving landscape of warehouse management solutions. Understanding the importance of implementing the right tools can greatly influence operational efficiency and visibility within a business. By optimizing inventory control and streamlining order fulfillment, Logiwa WMS can help businesses scale, adapt, and thrive in an increasingly competitive market.
Final Thoughts on Logiwa WMS
When you take a step back and assess the capabilities of Logiwa WMS, it quickly becomes clear that its versatility meets the needs of various industries. This software doesn’t just cater to e-commerce; it extends its arms to the manufacturing sector as well, providing functionalities that bridge gaps in operational processes. Companies can no longer rely on outdated methods; rather, embracing a robust system like Logiwa can lead to monumental shifts in productivity. The centralization of data allows for real-time updates, unlike older processes where discrepancies often led to confusion and even financial loss. In essence, Logiwa WMS starts as a tool but evolves into a strategic partner.
Next Steps for Businesses
Businesses looking to leverage the capabilities of Logiwa WMS should start by conducting an internal audit of their current systems. Here are actionable steps to consider:
- Assess Current Operations: Understanding where bottlenecks exist in your current warehouse setup.
- Research Integration Options: Evaluate how Logiwa WMS can work alongside existing software, especially ERP systems you might have in place.
- Engage Stakeholders: Involve team members in discussions to gather input and foster a culture of buy-in for the new system.
- Pilot Program: Consider running a pilot phase before a full rollout; this allows you to address hiccups without committing all resources.
- Training Sessions: Leverage Logiwa’s training materials to ensure that staff are comfortable with the new system from day one.
Implementing a WMS is not a trivial endeavor, but with a clear strategy and objectives in place, businesses can significantly enhance their operational framework.
In today's demanding marketplace, making informed decisions about warehouse management tools can dictate the trajectory of a business's success.
In summary, embracing Logiwa WMS is more than just installing software; it's about embarking on a journey toward improved efficiency and effectiveness that can fuel future growth.