Unleashing Zoho Inventory's Barcode Features
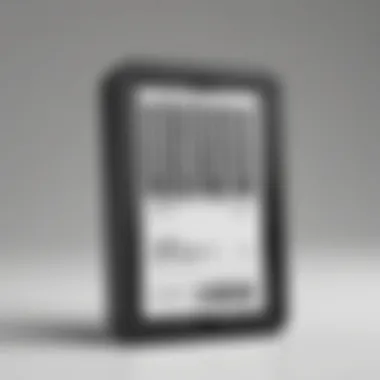
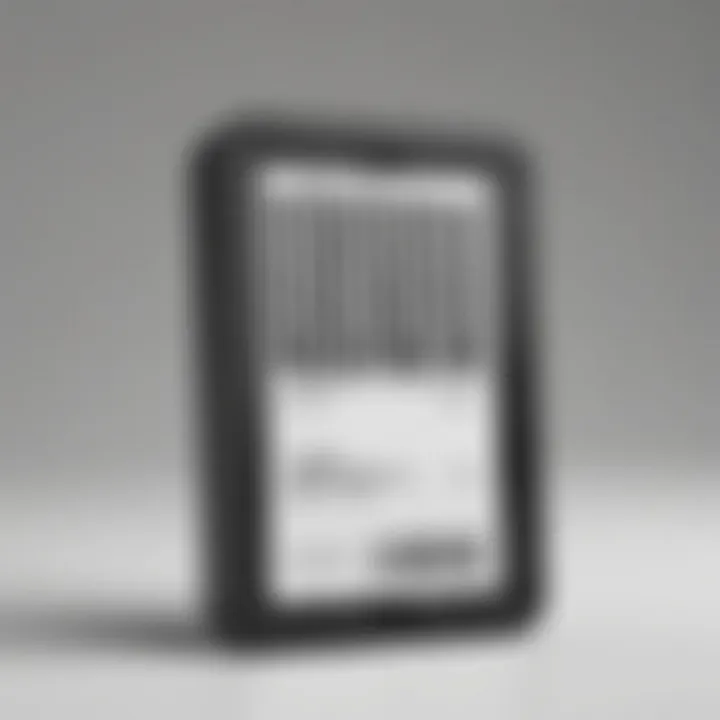
Intro
In todayβs competitive business environment, effective inventory management is vital. Companies often seek tools that can streamline operations. Zoho Inventory is one such solution offering comprehensive features. This article will look closely at its barcode functionality. This particular aspect is crucial for businesses aiming to improve their inventory tracking processes.
Utilizing barcode technology can significantly reduce human errors in stock management. It enhances accuracy and efficiency, especially for small to medium-sized businesses. Furthermore, understanding how to implement barcode scanning can help decision-makers choose the right tools to optimize their workflows.
Software Overview
Definition and Purpose of the Software
Zoho Inventory is an online inventory management software designed to help businesses track and manage stock in real-time. Its primary goal is to simplify the inventory process. By offering barcode functionalities, Zoho Inventory aids in accurately keeping records of products, shipments, and sales. This system is crucial for businesses that deal with a variety of products or services. It allows them to maintain control over their inventory levels while providing clear insights into their operational efficiency.
Key Features and Functionalities
The barcode functionality in Zoho Inventory plays a significant role. Below are some key features:
- Barcode Scanning: Quickly scan items for check-in and check-out, reducing time spent on manual entry.
- Barcode Label Printing: Generate custom barcode labels for products. This ensures a systematic approach to inventory tracking.
- Integration with Other Tools: Seamlessly integrates with shipping and sales software, allowing a unified view of inventory across platforms.
- Reporting and Analytics: Offers valuable insights through reports, helping businesses make data-driven decisions.
The benefits of these features enhance operational efficiencies and reduce loss due to errors.
Comparison with Alternatives
Overview of Competitors in the Market
Several other software solutions offer barcode functionalities. Notable competitors include TradeGecko, Fishbowl Inventory, and QuickBooks Commerce. Each provides unique features that caters to different business needs. Knowing how Zoho Inventory compares to these alternatives can guide businesses in making informed decisions based on their specific requirements.
Key Differentiators
Zoho Inventory stands out for several reasons:
- Affordability: Generally offers competitive pricing for small to medium-sized businesses.
- User-Friendly Interface: Designed for ease of use without compromising functionality.
- Comprehensive Customer Support: Provides solid customer service options, ensuring users can troubleshoot effectively.
"Maximizing inventory management through effective barcode scanning can transform operational workflows."
The combination of affordability, usability, and support allows Zoho Inventory to appeal strongly to small businesses. By understanding these differentiators, companies can better assess whether this software meets their specific needs.
Prologue to Zoho Inventory
In the realm of inventory management, proficiency with tools like Zoho Inventory stands as a pivotal advantage. This section aims to explore how Zoho Inventory not only simplifies inventory tracking but also integrates various features aimed at increasing operational efficiency. Businesses striving to optimize their inventory processes must recognize the significant role that technology plays in achieving these goals.
Understanding the complexities of managing inventory can be daunting. Many small to medium-sized business owners grapple with maintaining an accurate record of stock levels, order processes, and supplier relationships. Implementing software like Zoho Inventory provides clarity in these areas. It offers a suite of functionalities designed to facilitate smooth operations, thus allowing business leaders to focus more on strategic decision-making.
Understanding Inventory Management
Inventory management involves overseeing the flow of goods and materials in and out of a business. Several key tasks are associated with this process, including:
- Tracking inventory levels
- Monitoring stock locations
- Managing orders and suppliers
- Forecasting demand and replenishment
Failure to manage inventory effectively may lead to lost sales, overstock, or stockouts. These consequences can drastically affect a business's profitability. Therefore, a reliable inventory management system is vital. It aids in optimizing stock levels, reducing costs, and improving customer satisfaction. Zoho Inventory, with its advanced features, provides businesses the tools necessary for effective inventory oversight.
Role of Barcoding in Inventory
Barcoding serves as a crucial component in the realm of inventory management. It enhances accuracy and efficiency in tracking products. By affixing barcodes to inventory items, businesses can swiftly scan items for various operations, including:
- Receiving shipments
- Updating stock levels
- Processing sales
- Conducting audits
The implementation of barcodes mitigates human error, which often arises when entering data manually. Furthermore, it provides real-time visibility into inventory status, allowing for informed decision-making. A well-implemented barcoding system can streamline operations significantly, easing the burden on personnel and improving workflow overall.
Key Features of Zoho Inventory Barcoding
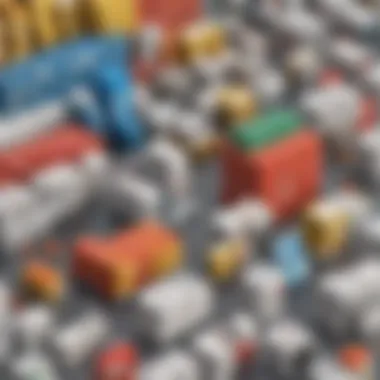
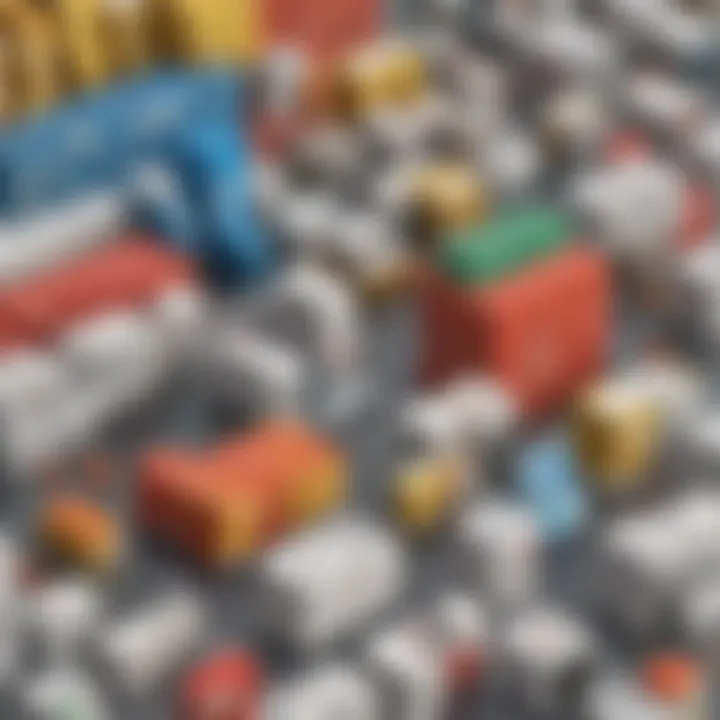
Zoho Inventory's barcoding functionality is designed to streamline inventory management for small to medium-sized businesses. Utilizing barcodes can significantly improve the accuracy and efficiency of tracking stock, reducing errors that often arise with manual entry. In this section, we will look at the specific features that distinguish Zoho Inventory's barcode capabilities. This insight is crucial for businesses looking to enhance their operational workflow and leverage technology effectively.
Barcode Generation
Barcode generation in Zoho Inventory facilitates the creation of unique identifiers for each inventory item. This process allows businesses to seamlessly track products throughout the supply chain. Users can generate various barcode formats, which include Code 39 and Code 128. Each format supports specific needs, making it versatile for different industries. Moreover, the barcode generation tool allows batch creation, enabling a swift setup for new products.
To optimize the inventory workflow, consider adopting a consistent naming convention for barcodes. This planning can mitigate confusion and ensure that each scanned item corresponds accurately to its records in the inventory system. Furthermore, being able to print barcodes in-house can save significant costs associated with outsourcing.
Scanning Capabilities
The scanning capabilities of Zoho Inventory are integral to efficient inventory management. The platform supports both dedicated barcode scanners and mobile devices equipped with scanning apps. This flexibility means that businesses can implement barcoding with existing hardware or invest in newer technologies as needed.
When employees scan items, the system instantly updates inventory levels, significantly reducing the need for manual input. This real-time interaction between physical stock and digital records minimizes discrepancies and improves data accuracy. Additionally, scanning items during logistics processes, such as receiving shipments or sales, enhances the speed of operations.
Itβs important to regularly test the scanning performance. Environment factors, such as lighting and the condition of barcodes, can impact the scanning efficiency. Ensuring that all devices are well-calibrated and that barcodes are printed clearly will enhance overall functionality.
Integration with Mobile Devices
Zoho Inventory's integration with mobile devices is an advanced feature that allows on-the-go inventory tracking. Users can utilize smartphones or tablets to scan barcodes, place orders, and manage stock levels from virtually anywhere. This capability is particularly beneficial for businesses with multiple locations or for those that operate in the field, as it provides real-time information right at their fingertips.
The mobile integration also facilitates the use of cloud storage. Data can be accessed and updated without the need for local storage limitations. This streamlining can enhance collaboration across teams, as updates on inventory levels can be shared instantly. Workers can update stock status or place orders directly from their devices, potentially increasing productivity and reducing delays in operations.
Benefits of Using Barcodes in Inventory Management
Barcodes serve a critical function in inventory management. They streamline processes and bring efficiency to operations. With advancements in technology, the adoption of barcoding has become increasingly essential for businesses of all sizes. This section will explore the specific benefits of integrating barcodes into inventory management practices.
Enhanced Accuracy
One of the foremost advantages of using barcodes is the improved accuracy in tracking inventory. Manual data entry often leads to errors. Employees may miscount items or input incorrect information. Barcodes eliminate these mistakes. Each barcode represents a unique identifier for products. When scanned, the system retrieves the correct data automatically. This minimizes the risk of human error significantly.
Enhanced accuracy not only improves day-to-day operations but also influences overall business strategies. Inaccurate inventory records can lead to overstocking or stockouts. These issues affect cash flow and customer satisfaction. A business that uses barcodes can maintain precise inventory levels, allowing it to fulfill orders promptly.
"Using barcodes can reduce data entry errors by over 50%, resulting in substantial cost savings and improved customer trust."
Increased Efficiency
The application of barcodes results in increased efficiency within inventory processes. When employees use barcode scanners, they can conduct tasks more quickly than when relying on manual methods. Scanning an item takes mere seconds, whereas typing product information requires more time.
Moreover, barcoding accelerates various inventory processes, such as receiving shipments or conducting stock audits. An item can be scanned upon arrival, updating the inventory in real time. This speeds up the onboarding of new products into inventory, allowing businesses to maintain a smooth operation.
Increased efficiency generates multiple benefits. Faster processing times lead to shortened lead times for customers. This advantage can improve customer loyalty, leading to repeat business. Additionally, reduced handling time decreases labor costs associated with inventory management.
Real-time Tracking
Real-time tracking is another significant benefit of implementing barcode technology. This function enables businesses to monitor inventory levels continuously. As items are sold or received, the inventory system updates immediately, providing accurate visibility.
Real-time tracking helps businesses identify trends and patterns in inventory turnover. For instance, it can reveal which products are selling faster than others. This information allows for better purchasing decisions, ensuring businesses stock the right items to meet demand. Moreover, it enhances reporting capabilities, facilitating precise forecasting and planning.
In summary, the benefits of using barcodes in inventory management significantly impact operational effectiveness. Enhanced accuracy, increased efficiency, and real-time tracking are core advantages. These factors create a competitive edge in today's fast-paced market. Implementing barcodes is crucial for small to medium-sized businesses aiming to optimize their inventory systems.
How to Implement Barcoding in Zoho Inventory
Implementing barcoding in Zoho Inventory is a vital step for businesses aiming to enhance their inventory management process. Barcoding simplifies the checking, tracking, and managing of stock. It also reduces human errors associated with manual entry. In this section, we will cover its fundamental components, benefits, and what to consider during setup.
Implementing barcoding is not just about scanning items; it involves strategic planning and execution. Businesses must ensure that they have a clear understanding of the existing system. Furthermore, aligning team members with the operational changes will foster a smoother transition. With the right approach, barcoding positions a business to improve efficiency and accuracy.
Setting Up Barcode Preferences
Setting up barcode preferences in Zoho Inventory is a crucial first step. This process begins in the settings menu. Users should navigate to the 'Barcode Settings' section. Here, they can select their preferred barcode format, such as Code 128 or QR codes. Each format may have specific use cases that align better with certain inventory items.
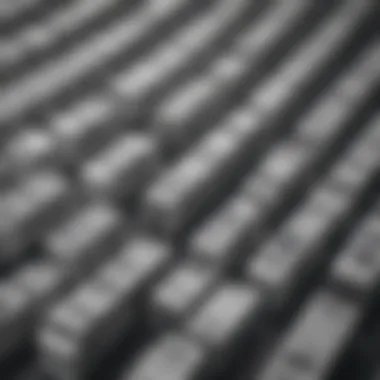
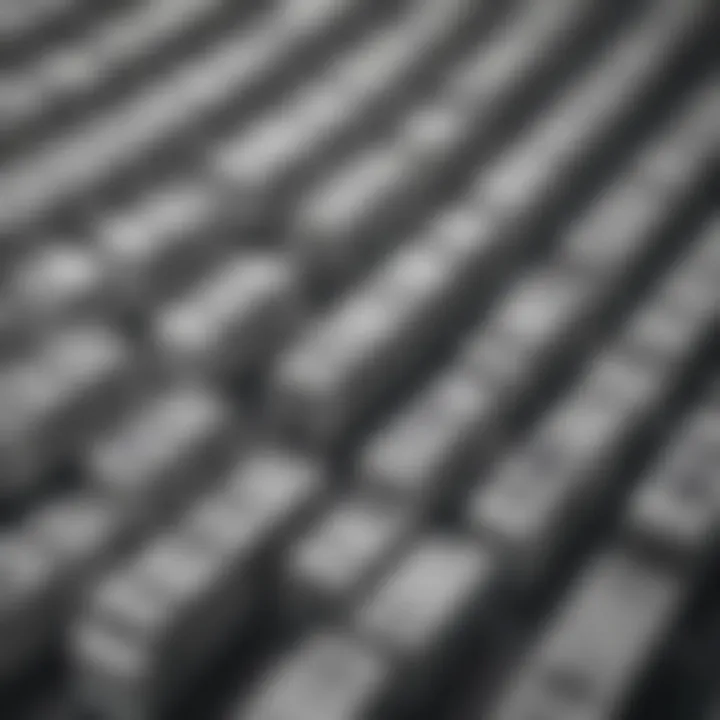
After determining the format, businesses must decide on the structure of the barcode data. This could involve incorporating SKU numbers or item descriptions. Clear decision-making here helps eliminate future confusion during scanning processes.
Ensuring that barcode preferences are set correctly can structure inventory operations more effectively. A well-defined setup leads to seamless inventory tracking and easier integrations down the line.
Adding Barcodes to Inventory Items
Adding barcodes to inventory items in Zoho Inventory streamlines the management process. Users can do so by accessing the item list. For each item, there is an option to input the barcode. Here, manual entry is possible, along with uploading from a file, facilitating bulk additions.
It is essential to verify that each item has a unique barcode assigned. Duplicate barcodes can lead to scanning errors and inaccurate stock levels. Data entry should maintain consistency matching the previously set barcode preferences.
Once added, these barcodes can enhance visibility in stock levels and availability. This step also enables reporting and analytics functions to identify trends and inefficiencies, providing critical insights into inventory performance.
Conducting Inventory Audits with Barcodes
Conducting inventory audits becomes significantly easier with barcodes implemented. Typically, audits include checking stock levels against recorded quantities. Scanning barcodes allows for quick verification, drastically reducing the time needed compared to manual counting.
To perform audits effectively, businesses should prepare a checklist of items to be verified. Using handheld scanners or mobile devices, each item is scanned directly. The system updates in real-time, allowing discrepancies to be recorded immediately. This precision ensures that any missing stock or overages can be addressed promptly.
It's important to establish a routine for audits. Regular audits help maintain inventory integrity and assure compliance with best practices. They also enhance overall trust in the inventory data collected over time.
Regular audits not only verify stock levels but also identify shrinkage or other issues that could affect profitability.
Integrating Zoho Inventory with Other Software Solutions
Integrating Zoho Inventory with other software solutions is critical for businesses looking to streamline their operations. Efficient data flow between systems eliminates the need for manual data entry, which reduces errors and saves valuable time. By ensuring that your inventory management software works synergistically with other tools, businesses can achieve not only operational efficiency but also better data-driven decision-making.
Compatibility with Accounting Software
A key aspect of integrating Zoho Inventory is its compatibility with accounting software. Most businesses use accounting software to manage their finances, track expenses, and generate reports. When Zoho Inventory integrates seamlessly with popular accounting platforms like QuickBooks or Xero, it allows for automatic updates of financial records based on inventory changes. This real-time synchronization is important for several reasons:
- Accuracy: Automated entries minimize human error related to manual data handling.
- Time-saving: Accounts do not need manual updates after each inventory sale.
- Financial Planning: Accurate inventory values help in better forecasts and budget management.
In this context, the integration also ensures compliance with accounting standards by providing clear documentation of all transaction types. Seamless communication between inventory management and financial reporting is vital for small to medium-sized businesses.
Linking with E-commerce Platforms
Linking Zoho Inventory with e-commerce platforms is another significant area of integration. For businesses that operate online, it is essential that inventory levels are synchronized across all sales channels. When Zoho Inventory is connected to platforms such as Shopify or WooCommerce, it allows for:
- Real-time Updates: Inventory levels are automatically updated to reflect current stock, helping avoid overselling.
- Holistic View: Business owners gain visibility into both online and offline inventory, which aids in resource allocation.
- Improved Customer Experience: Customers can receive accurate information concerning product availability, enhancing their shopping experience.
Additionally, an integrated system can assist with order fulfillment processes. As orders come in through the e-commerce portal, they can trigger inventory adjustments in Zoho Inventory without requiring separate manual actions.
CRM Integration Benefits
The integration of Zoho Inventory with Customer Relationship Management (CRM) systems provides extra layers of benefits for managing customer interactions. When Zoho Inventory is linked to CRMs like Zoho CRM or Salesforce, businesses can:
- Enhance Customer Insights: Combining sales and inventory data provides better understanding of buying patterns, which helps in targeting customers effectively.
- Streamline Sales Process: Sales teams have access to up-to-date inventory levels, allowing them to confidently assure customers about product availability.
- Personalized Service: Insights from both inventory and CRM enable personalized marketing efforts and relationship building with clients.
All of these integrations combined lead to a more unified approach to managing operations. The flow of information between Zoho Inventory and these essential systems ensures that businesses can operate smoothly, adapt quickly to changes, and ultimately provide a better experience for their customers.
"Integrating different software solutions creates a comprehensive ecosystem that can adapt to the dynamic needs of modern businesses."
Best Practices for Effective Barcode Usage
Effective barcode usage is essential for enhancing the operational efficiency of inventory management. Implementing best practices ensures that businesses can maximize the benefits of barcoding technology while minimizing potential errors. This section highlights the critical components of effective barcode usage, including maintaining barcode quality, conducting regular system updates, and training staff adequately on barcode application.
Maintaining Barcode Quality
Maintaining the quality of barcodes is paramount for ensuring accurate scanning and data retrieval. High-quality barcodes are easier to read and less prone to scanning issues. For small to medium-sized businesses, consistent monitoring of barcode quality can prevent costly mistakes in inventory management. Regular inspections can be implemented to detect and replace damaged labels or print errors in barcodes. Using high-resolution printers and durable materials can also improve barcode longevity. By investing in quality control measures,
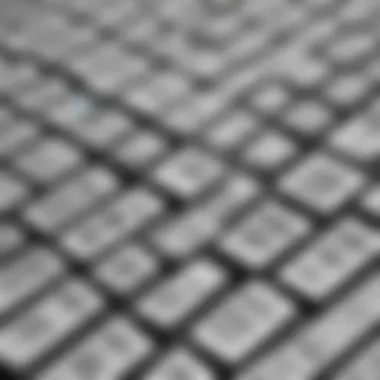
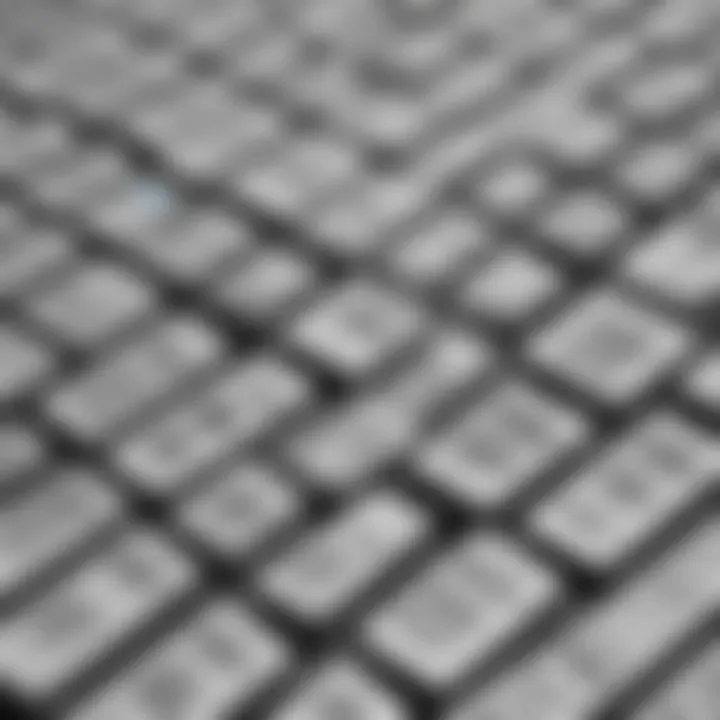
- Use barcode labels that are resistant to wear and moisture. This prevents degradation over time.
- Perform regular audits of barcode scans to identify any discrepancies in item readings.
- Consider using QR codes for complex datasets where traditional barcodes may fall short.
Maintaining barcode quality directly influences inventory accuracy and efficiency.
Regular System Updates and Maintenance
Regular system updates are crucial for the effective functioning of barcode systems. Software solutions like Zoho Inventory often have new features or security updates that improve performance and reduce vulnerabilities. Schedule periodic check-ups for system maintenance, ensuring that all software components are current. This can also include:
- Updating barcode scanners and software to the latest versions.
- Verifying compatibility with new operating systems or platforms when integrating with other software solutions.
- Backing up data regularly to prevent loss from system failures.
By prioritizing system updates and maintenance, businesses safeguard their barcode functions against unforeseen issues.
Training Staff on Barcode Usage
Effective training is a foundation for successful barcode implementation. Employees must understand how to use barcode scanners, recognize common issues, and troubleshoot effectively. A comprehensive training program should cover:
- Basic functionality of barcode scanners including scanning techniques and device handling.
- Common challenges like mis-scanning and how to resolve them promptly.
- Using the underlying software to track inventory accurately using barcodes.
Regularly update training materials to reflect changes in technology and processes. Investing time in training leads to:
- Increased employee confidence when handling inventory.
- Reduced errors during the scanning process, which translates to better accuracy.
- Enhanced overall productivity as staff becomes proficient in using barcoding systems.
Potential Challenges and Solutions
In any business implementation of technology, the path is rarely smooth. Barcoding, while incredibly beneficial for inventory management, presents its own set of challenges. Understanding these challenges and knowing how to address them can significantly affect the success of using Zoho Inventory's barcode functionality. This section will explore common issues that businesses face, as well as the solutions available to mitigate these problems.
Common Barcode Scanning Issues
One of the most frequent challenges encountered in barcode scanning is the failure to read the barcode correctly. This can happen for various reasons, such as dirt or damage on the barcode itself, or issues with the scanning hardware. If a barcode is not clean or is partially obscured, scanners may struggle to decode it. Additionally, low-quality barcodes may not meet the necessary resolution for accurate scanning.
To tackle these problems, maintain the barcodes in good condition through regular cleaning and inspections. Using higher-quality labels can also reduce defects. Furthermore, ensuring that the scanning equipment is of good quality and properly calibrated is crucial. Training staff on proper scanning techniques can address many operational errors.
Data Synchronization Problems
In a dynamic inventory environment, data synchronization is vital. However, delays and inconsistencies can occur, especially when integrating Zoho Inventory with other systems. These synchronizing issues can lead to discrepancies in inventory levels, making it challenging to maintain accurate records.
To avoid such issues, it is essential to configure the integration properly and ensure regular updates are performed across all systems involved. Automation tools can also assist in maintaining data integrity by providing real-time updates. Moreover, regularly reviewing synchronization logs can help quickly identify and correct problems.
Addressing User Adaptation Issues
The implementation of barcode technology may present a steep learning curve for some employees. Resistance to change, lack of training, and comfort with previous methods can hinder the adoption process. Employees may feel overwhelmed with the new processes or unsure about how to utilize the technology effectively.
To combat this resistance, providing comprehensive training sessions is essential. Encourage a culture of learning where questions are welcomed. For instance, creating a user manual or resources for employees to refer back to can be beneficial. Offering ongoing support, even after implementation, is vital to help users adapt more smoothly.
"Investing in user training and support can have exponential returns in productivity and accuracy."
By identifying these challenges and considering proactive solutions, businesses can significantly enhance their experience with Zoho Inventory's barcode functionalities. This not only streamlines their inventory processes but also contributes to overall operational efficiency.
The Future of Barcoding in Inventory Management
As businesses evolve, the need for better and more efficient inventory management systems increases. Barcoding is becoming increasingly integral to this process. Looking ahead, barcoding technology stands to reshape how businesses manage inventory. It offers a path to greater accuracy, efficiency, and adaptability in a rapidly changing marketplace.
Emerging Technologies in Inventory Management
Emerging technologies significantly impact inventory management. Technologies like RFID (Radio Frequency Identification) and IoT (Internet of Things) are making their way into barcoding practices. RFID technology allows for faster scanning and accuracy compared to traditional barcodes. With IoT, devices can communicate and share real-time data across systems. This technology aims to minimize human error and enhance the overall tracking of inventory items. As these technologies improve, they will redefine barcoding standards and operations in the future.
AI and Machine Learning Integration
AI and machine learning are promising additions to barcoding systems. These technologies can analyze large datasets to optimize inventory levels and reduce excess stock. AI can predict trends based on past data, potentially leading to smarter inventory decisions. Machine learning algorithms can also improve barcode scanning and recognition over time. Integrating AI with Zoho Inventory could enhance its barcode capabilities and provide actionable insights, helping businesses operate more efficiently.
Advances in Mobile Technology
Mobile technology continues to transform inventory management. Smartphones and tablets are now equipped with advanced scanning capabilities. Apps can easily scan barcodes and integrate directly with inventory software, such as Zoho Inventory. These advances make it easier for businesses to access real-time inventory data and enable field workers to update inventory systems on the go. Future enhancements in mobile technology will likely focus on increasing speed and precision in scanning, making processes even more seamless.
"By integrating advanced technologies into barcoding systems, businesses can stay ahead of the increasingly complex demands of inventory management."