Top CMMS Systems: Comprehensive Overview & Analysis
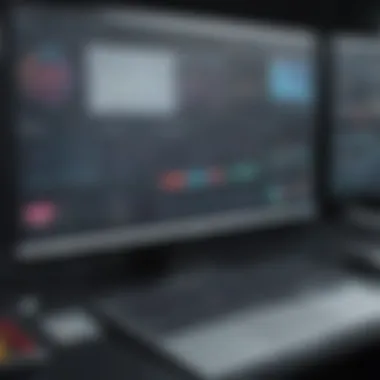
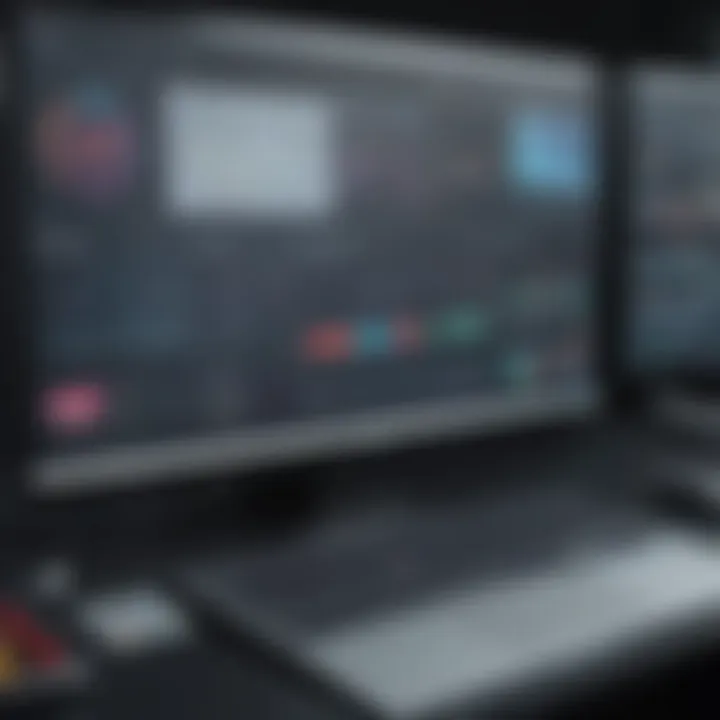
Intro
The landscape of maintenance management systems is witnessing a significant transformation. Computerized Maintenance Management Systems (CMMS) have become indispensable for businesses seeking to streamline their maintenance operations. These systems provide tools to manage work orders, track equipment performance, and analyze maintenance dataโall crucial for enhancing operational efficiencies.
Investing in the right CMMS can dramatically affect an organizationโs productivity and its overall operational success. Yet, with myriad options available, determining which system is best suited for specific business needs can be complex. This analysis aims to demystify the top solutions on the market today, offering insights into their features, usability, and overall economic viability.
Preamble to CMMS
In todayโs fast-paced business environment, maintenance management plays a crucial role in operational success. Computerized Maintenance Management Systems (CMMS) offer systematic approaches to manage maintenance activities effectively. This introduction sets the stage for understanding the significance of CMMS in maintaining assets, controlling costs, and enhancing overall productivity.
Definition and Purpose of CMMS
A CMMS is software designed to streamline maintenance management by automating various tasks related to asset maintenance. Its primary purpose is to provide a centralized platform for monitoring and managing maintenance operations. Users can track work orders, schedule preventive maintenance, and manage inventory efficiently within one system.
By implementing a CMMS, companies can ensure that all maintenance tasks are organized and completed in a timely manner. This leads to increased equipment longevity, reduced downtime, and ultimately, greater profitability. Moreover, it allows businesses to make data-driven decisions, supporting strategic planning and resource allocation.
Importance of CMMS in Business Operations
The integration of a CMMS into business operations is vital for several reasons. First, it directly impacts asset performance by ensuring consistent maintenance routines. Equipment that is regularly maintained tends to operate more efficiently and has a longer life span. This not only keeps production lines moving but also reduces the costs associated with repairs and replacements.
Another significant benefit of a CMMS is its contribution to safety. Well-maintained machinery reduces the risk of accidents. If employees work in a safe environment, it can result in lower insurance premiums and minimized liability issues. Additionally, compliance with industry regulations is easier when maintenance records are organized and easily accessible.
"An effective CMMS can transform a reactive maintenance strategy into a proactive one, allowing businesses to solve maintenance issues before they escalate."
Furthermore, CMMS systems improve communication among team members. With all maintenance data stored in one place, it becomes easier for maintenance personnel and management to collaborate. This leads to better decision making and helps in training new staff effectively.
In summary, understanding CMMS is essential for any organization aiming for operational excellence. As we delve deeper into the features and advantages of different CMMS solutions, it becomes evident that these systems are more than just tools; they are integral to high-performing maintenance strategies.
Key Features of CMMS Systems
Computerized Maintenance Management Systems (CMMS) play a pivotal role in simplifying maintenance processes for various organizations. An effective CMMS must integrate several key features that address the unique needs of its users. These features are not merely functional; they provide numerous benefits that can enhance overall operational efficiency. Emphasizing the right features can significantly influence an organizationโs maintenance strategy and lead to improved productivity.
Asset Management
Asset management is one of the core functionalities of a CMMS. It allows businesses to keep a comprehensive record of all their assets. This includes information on asset location, condition, and maintenance history. By utilizing an asset management feature, companies can track the lifecycle of their equipment. This enables them to make informed decisions regarding repairs, replacements, and overall asset utilization. Moreover, it helps in reducing downtime by ensuring that regular maintenance is performed as needed.
Work Order Management
Work order management streamlines the workflow associated with maintenance tasks. With this feature, users can create, assign, and track work orders from initiation to completion. Work orders can include detailed task descriptions, deadlines, and assigned personnel. This enhances accountability and ensures that all team members are aware of their responsibilities. By centralizing work order information, organizations can monitor progress and identify bottlenecks. This leads to more effective resource allocation and helps maintain productivity.
Inventory Management
An effective inventory management feature within a CMMS is crucial for ensuring that the right parts and supplies are available when needed. This feature allows businesses to track inventory levels, manage suppliers, and forecast future needs based on maintenance schedules. By maintaining optimal inventory levels, companies can avoid overstocking or stockouts. Additionally, improved inventory management can reduce holding costs, allowing resources to be allocated more efficiently.
Reporting and Analytics
Reporting and analytics play a significant role in enhancing the decision-making process for organizations. A robust CMMS should offer a variety of customizable reports. This includes data on asset performance, maintenance costs, and work order efficiency. By analyzing this data, organizations can identify trends and areas for improvement. For example, if a specific asset frequently requires repairs, it may indicate the need for replacement or more frequent maintenance. Data-driven insights empower businesses to fine-tune their maintenance strategies and optimize performance.
"Understanding key features of a CMMS is fundamental for small to medium-sized businesses aiming to enhance maintenance processes and drive operational efficiency."
The integration of these key features makes CMMS systems indispensable for modern maintenance management. As companies continue to prioritize efficiency and effectiveness, the significance of these functionalities will only increase. By leveraging asset management, work order management, inventory management, and reporting capabilities, organizations can transform their maintenance workflows into streamlined, productive processes.
Evaluating the Top CMMS Systems
To make an informed decision when choosing a Computerized Maintenance Management System (CMMS), evaluating the available options is crucial. This evaluation process helps in understanding the distinct features and functionalities of different systems. By grasping these elements, businesses can align their operational goals with the capabilities of a CMMS. This should ultimately lead to enhanced maintenance efficiency and improved resource management. Through well-defined criteria, organizations can assess the systems more effectively, ensuring the selected solution meets their specific needs.
Criteria for Evaluation
When evaluating CMMS options, several criteria should be considered. These factors directly impact the effectiveness of the system in a business environment. They include:
- Usability: The interface should be user-friendly. A system that requires extensive training can slow down operations.
- Scalability: It is important to choose a CMMS that can grow with the business. This allows for effective management of increasing assets and maintenance tasks.
- Integration capabilities: The ability of a CMMS to integrate with existing enterprise systems, such as ERP or financial software, is vital. This ensures seamless data flow and enhances operational efficiency.
- Customization options: A degree of flexibility in tailoring the system to meet unique business processes can be beneficial.
- Customer support: Reliable support services can assist in troubleshooting and maximizing system utility.
- Cost-effectiveness: The price of the system needs to align with its value. Transparent pricing structures should be considered to avoid hidden costs.
Evaluating CMMS against these criteria allows for a holistic overview, helping businesses identify which systems are most viable for their operations.
Market Trends and Developments
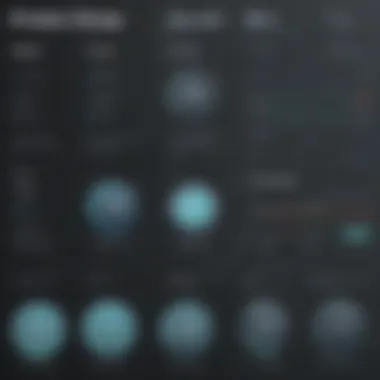

The landscape of CMMS is constantly changing. Staying updated with current market trends is essential for business decision-making. Some notable developments include:
- Cloud-based solutions: More businesses are adopting cloud-based CMMS due to their cost-effectiveness and accessibility. Data can be accessed from anywhere, facilitating remote maintenance management.
- Mobile applications: Growing demand for mobile access enables technicians to manage tasks and respond to work orders on the go. This immediacy improves response times and accountability.
- Predictive maintenance: With advancements in AI and machine learning, predictive maintenance is becoming more common. CMMS systems can analyze data trends to predict equipment failures before they occur, leading to significant uptime improvements.
- Data analytics: Enhanced reporting and analytics capabilities allow businesses to make data-driven decisions. This analysis helps in streamlining maintenance activities, ultimately leading to better performance outcomes.
Understanding these trends is vital for businesses when selecting a CMMS. This knowledge ensures that they are not only choosing a system that works today but also one that can adapt to future requirements and technologies.
"Evaluating CMMS systems thoroughly helps businesses leverage the right tools for optimal maintenance management."
Overview of Leading CMMS Solutions
Computerized Maintenance Management Systems (CMMS) play a pivotal role in optimizing maintenance processes within organizations. The leading CMMS solutions available today are designed to enhance efficiency, reduce costs, and improve overall operations. This section will delve into the significance of these leading systems, providing insight into their specific elements, benefits, and the nuances that differentiate them in the market.
Details of Top CMMS Systems
Analyzing the details of the top CMMS systems can provide critical information for decision-makers in any organization. Each system brings unique features and capabilities, designed to cater to various maintenance needs. Here, we will examine ten prominent systems across various dimensions including user experience, cost, and functionality.
System One Overview
System One is known for its user-friendly interface, which greatly contributes to its popularity among small to medium-sized businesses. Its ease of use allows for quick deployment and training, minimizing the learning curve for staff. A notable feature of System One is its mobile accessibility, enabling technicians to access information and manage tasks remotely. This feature translates to improved response times and enhanced workforce productivity, making it a valuable asset for any maintenance team.
System Two Overview
System Two stands out due to its comprehensive analytics capabilities. This feature allows users to track key performance indicators effectively. The systemโs robust reporting tools give insights into maintenance trends, which aid in planning future maintenance activities. Organizations that emphasize data-driven decisions find System Two especially beneficial. However, its complexity in setup may require dedicated resources for an optimal implementation experience.
System Three Overview
Offering strong asset management features, System Three is praised for its ability to integrate seamlessly with other enterprise systems. It is a beneficial choice for organizations looking to streamline workflows. The standout aspect of this system is its automated maintenance scheduling, which prevents equipment downtime. However, potential users should consider the initial cost implications associated with system integration.
System Four Overview
System Four is often recognized for its scalability, making it suitable for growing businesses. The key characteristic of this system is its flexible pricing model, which adjusts according to usage. This adaptability allows companies to expand their maintenance management capabilities without a substantial upfront investment. One unique feature here is its ability to integrate with IoT devices for predictive maintenance, although some users may encounter challenges with system updates.
System Five Overview
Focusing on user interaction, System Five features an intuitive dashboard that simplifies navigation. This design choice enhances the overall user experience and encourages frequent engagement with the platform. The real-time monitoring capabilities allow organizations to respond swiftly to issues. Nevertheless, organizations aiming for extensive customization may find limitations in available modifications.
System Six Overview
System Six is particularly noted for its customer support and training programs. Organizations new to CMMS benefit significantly from the comprehensive training resources available. The maintenance history tracking aspect is particularly useful for assessing equipment longevity and performance. On the downside, some users report slow response times from support during high-demand periods, a factor that should be evaluated prior to commitment.
System Seven Overview
The automated inventory management of System Seven sets it apart as a strong contender for businesses that manage significant physical assets. The key feature of this system is its just-in-time inventory capabilities, which align stock levels with operational needs. While this leads to cost savings on inventory holding, the detailed configuration and constant monitoring required may necessitate dedicated personnel.
System Eight Overview
System Eight is well-regarded for its cloud-based offering, making it accessible from anywhere. The ability to facilitate collaboration between teams is a significant benefit. The integration with third-party applications is a highlighted feature, benefiting organizations that use multiple software. However, it is essential to note the potential for increased costs associated with data storage as usage scales up.
System Nine Overview
For organizations prioritizing compliance, System Nine presents robust regulatory features. It assists in meeting industry standards, which can be crucial in sectors like healthcare or manufacturing. The audit tracking functionalities provide transparency in operations, although this may also result in a steeper learning curve for users unfamiliar with regulatory compliance.
System Ten Overview
Lastly, System Ten targets large enterprises with its advanced customization options. It stands out for its ability to adapt to complex structures and workflows. The system provides multi-site management features which are ideal for businesses operating in various locations. However, potential users should prepare for a significant investment and the time needed for a comprehensive setup and training process.
"Choosing the right CMMS system can significantly enhance maintenance efficiency and asset management capabilities. Understanding the strengths and weaknesses of each system is crucial."
System One: A Case Study
In the landscape of Computerized Maintenance Management Systems (CMMS), analyzing specific systems allows businesses to glean practical insights. System One serves as a compelling case study due to its robust feature set and adaptability to various industries. This section highlights its significance, focusing on key elements like user experience, capabilities, and implementation considerations.
Key Features and Benefits
System One is designed to streamline maintenance operations efficiently. Some of its key features include:
- User-Friendly Interface: The intuitive design enables quick onboarding for new users.
- Real-Time Monitoring: Users can track equipment performance in real time, which aids in proactive maintenance.
- Mobile Accessibility: The mobile app ensures that technicians can access information and update statuses from the field.
- Integrative Capability: System One can easily integrate with other enterprise systems, which enhances workflow.
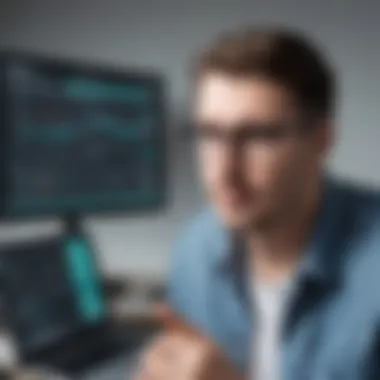
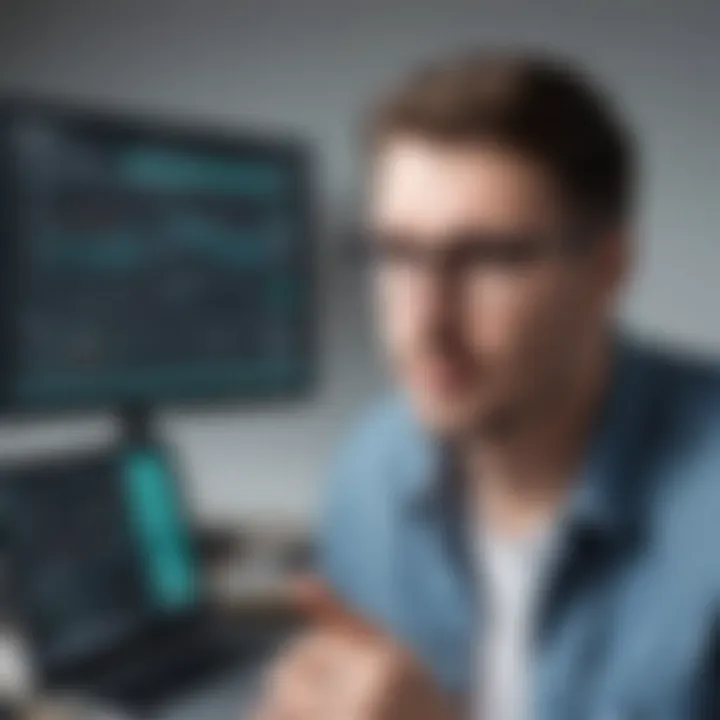
The benefits of these features are profound. Staff can improve productivity through easier information access. Also, real-time monitoring minimizes downtime by enabling rapid response to potential issues. The focus on mobile access means that teams are not tied to a desk, creating more flexibility in job management.
User Feedback and Case Studies
User feedback on System One has been predominantly positive. Many users appreciate the straightforward setup process and ongoing support provided by the vendor. For instance, a case study of a mid-sized manufacturing plant using System One noted significant improvement in their maintenance response time. The facility reduced equipment downtime by 30% within the first six months of implementation.
"We were astonished with how quickly our team adapted to System One. The immediate impact on our efficiency is undeniable," shared the maintenance manager from the manufacturing plant.
However, some users mention challenges in data migration during the initial setup. Proper planning and consultation with System Oneโs support teams help mitigate these issues, ensuring seamless transitions for new users.
Cost and Implementation Considerations
When evaluating the financial aspects of System One, it's crucial to consider both initial costs and long-term value. The pricing model is subscription-based, allowing businesses to opt for plans that fit their budgets. Users often report that the ROI becomes evident through the improved efficiency in maintenance operations.
Implementation considerations include:
- Training and Support: Adequate training sessions are essential for user adoption and maximizing system features.
- Customization: System One offers options for customization based on specific industry needs. This can affect the implementation timeline and cost.
- Scalability: As businesses grow, System One can scale with their needs, making it a long-term investment in operational efficiency.
In summary, System One exemplifies how a CMMS can enhance maintenance management's efficacy through user-focused features and strategic implementation.
System Two: A Case Study
System Two represents a significant development in the field of Computerized Maintenance Management Systems (CMMS). This case study offers a window into its functionalities and how it addresses common maintenance challenges faced by organizations today. Understanding this system allows businesses to grasp its value in streamlining operations, enhancing efficiency, and leading to better asset management.
Key Features and Benefits
System Two is designed with a variety of features that cater specifically to the needs of maintenance professionals. Among these features, the following stand out:
- User-Friendly Interface: The layout is intuitive, which minimizes the learning curve for new users.
- Mobile Accessibility: Users can access the system from mobile devices, allowing for on-the-go management and decision-making.
- Real-Time Monitoring: This feature lets users track asset performance continuously, aiding in timely maintenance actions.
- Custom Reporting: System Two allows users to generate reports tailored to their needs, which can help in identifying trends and areas for improvement.
The benefits of these features are numerous. For instance, real-time monitoring leads to a reduction in equipment downtime. Moreover, the ability to access the system remotely promotes flexibility and enables quick responses to maintenance requests.
User Feedback and Case Studies
Feedback from users of System Two highlights its effectiveness in various operational environments. Many report increased productivity due to the automation of maintenance scheduling.
Case studies have corroborated this positive impact. For example, a manufacturing company documented a 30% reduction in maintenance response times after implementing System Two. Additionally, users appreciate the strong customer support, which is a crucial element when troubleshooting issues during implementation.
"With System Two, we have achieved unseen levels of operational efficiency. Scheduling has never been easier!"
โ Operations Manager, Manufacturing Company
Cost and Implementation Considerations
Cost is always a vital factor when selecting a CMMS. System Two offers various pricing tiers, making it accessible for small to medium-sized businesses. However, it is crucial to consider not just the subscription cost but also the potential return on investment. With enhanced efficiency and reduced downtime, many users find that the overall savings justify the expense.
When planning implementation, businesses need to assess their readiness for change. This includes staff training and the integration of existing systems with System Two. The transition may require initial time and resources, but the long-term benefits often outweigh these early challenges.
Comparative Analysis of CMMS Systems
In today's competitive landscape, selecting the right Computerized Maintenance Management System (CMMS) is critical for small to medium-sized businesses. A comparative analysis of CMMS systems serves as a foundational step in distinguishing their strengths and weaknesses. This section will illuminate the key factors that businesses should consider when evaluating various CMMS options. Moreover, it offers insights into the multiple dimensions that can significantly influence operational efficiency.
Feature Comparison
When businesses evaluate CMMS systems, features often take center stage. Each system varies in functionalities such as asset management, work order management, reporting capabilities, and user interface. A thorough feature comparison can highlight these distinctive offerings, allowing stakeholders to match their needs with the right software.
Consider key features that often include:
- Asset Management: How effectively does the CMMS track assets, their condition, and lifecycle?
- Work Order Management: Is the process for creating, tracking, and closing work orders intuitive and efficient?
- Inventory Management: How does the system handle parts and supplies? Is there a built-in inventory tracking system?
- Reporting and Analytics: What insights can users gain through reporting tools? Are the analytics options robust enough for decision-making?
Establishing a clear understanding of these specific elements will directly impact the potential productivity and cost-effectiveness of maintenance operations.
Cost Comparison
The financial aspect of implementing a CMMS cannot be overstated. Different systems come with varied pricing structures, from subscription models to one-time licensing fees.
A cost comparison should encompass:
- Upfront Costs: What initial investments are necessary for hardware and software?
- Recurring Costs: What are the monthly or annual maintenance and subscription fees?
- Long-term Value: Does the systemโs ROI justify the costs associated?
- Hidden Fees: Are there costs associated with updates, training, or customer support that may not be immediately apparent?
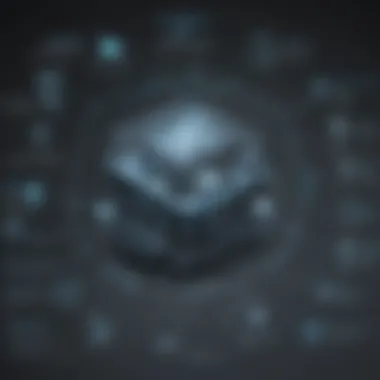
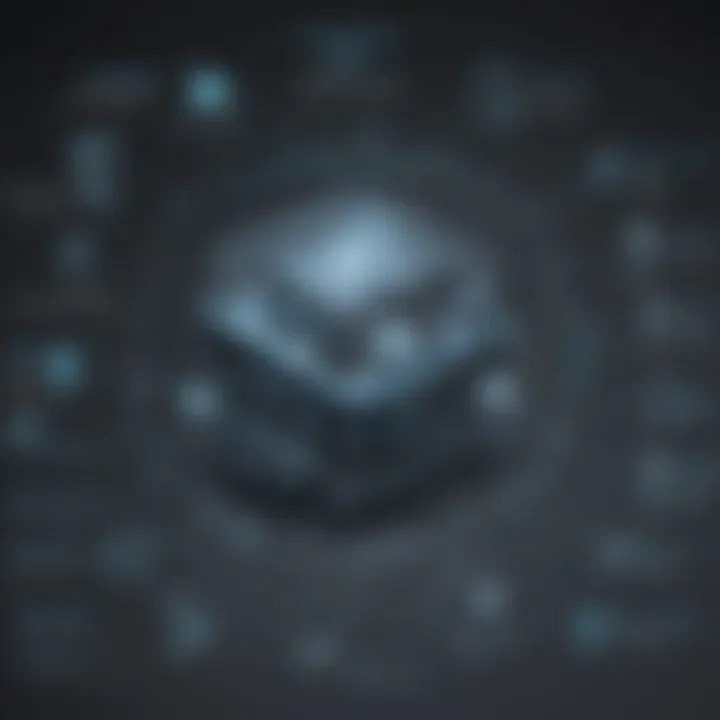
By analyzing these financial elements, businesses can better understand the true cost of ownership and make informed decisions.
User Experience Comparison
User experience is often the determining factor in the successful adoption of a CMMS. A positive user experience can facilitate smoother training sessions and higher overall satisfaction among users.
Key aspects to evaluate include:
- Ease of Use: How intuitive is the system? Can users navigate without extensive training?
- Customer Support: What level of customer service is available? How responsive is the support team?
- Customization Options: Can the system be tailored to fit specific business processes or industries?
- Feedback from Current Users: What are actual users saying about their experiences? Are there common themes in user reviews?
Gathering insights on user experience can help identify potential pitfalls and advantages of each system.
Challenges in CMMS Implementation
Implementing a Computerized Maintenance Management System can bring many advantages. However, organizations often face several challenges that can hinder this process. Understanding these challenges is crucial for achieving successful CMMS integration. Addressing issues early can facilitate smoother transitions and greater acceptance among staff. This section discusses the common barriers to adoption and solutions to overcome them.
Common Barriers to Adoption
Adoption of CMMS is not without its obstacles. Several specific barriers can slow down or derail implementation efforts.
- Resistance to Change: Employees may be accustomed to existing processes. They might view a shift to new technology as unnecessary or intimidating.
- Insufficient Training: Many businesses fail to provide adequate training for users. When staff do not fully understand the system, they may struggle to adapt.
- Integration Issues: Existing systems may not seamlessly connect with the new CMMS. This lack of compatibility can lead to data silos, increasing user frustration.
- Cost Concerns: Small to medium-sized businesses often worry about the expenses associated with CMMS. Budget constraints may limit software options and reduce necessary resources for implementation.
- Lack of Leadership Support: If high-level management does not prioritize CMMS, it can lead to a lack of engagement among staff. Employees need to see commitment from leadership to get on board with a new system.
"Understanding common barriers to CMMS adoption can help businesses prepare and implement successful change strategies."
Strategies for Effective Implementation
To navigate these challenges, organizations can adopt various strategies for effective implementation of CMMS. A planned approach can increase the likelihood of achieving desired results.
- Engage Leadership Early: Secure buy-in from management. Their support is essential for fostering a more positive attitude among employees.
- Conduct Comprehensive Training: Invest time in training sessions tailored to staff needs. Encourage hands-on learning to improve confidence in using the system.
- Focus on Integration: Assess existing systems and determine compatibility before selecting a CMMS. Choose a solution that allows for easy data exchange to minimize disruptions.
- Start with a Pilot Program: Implement the system in a smaller department first. Gather feedback to make necessary adjustments before full-scale rollout.
- Continuous Support and Feedback: Establish channels for ongoing support. Encourage users to provide feedback, allowing for timely adjustments and improvements.
Future Trends in CMMS Development
The exploration of future trends in Computerized Maintenance Management Systems (CMMS) is essential for businesses aiming to maintain relevance in an ever-evolving technological landscape. Understanding these trends allows professionals to adapt and optimize maintenance processes.
Emerging Technologies
Emerging technologies are reshaping the landscape of CMMS. Technologies such as Internet of Things (IoT), augmented reality (AR), and cloud computing are significantly enhancing the capabilities of these systems.
- Internet of Things (IoT): IoT devices facilitate real-time monitoring of assets. Connected sensors collect data which helps in identifying maintenance needs proactively. This leads to more efficient operations and reduced downtime.
- Augmented Reality (AR): AR technology enables remote assistance for maintenance technicians. It allows specialists to view equipment components in 3D overlays, helping them perform tasks more effectively. This can be particularly advantageous in training scenarios, reducing the learning curve for new employees.
- Cloud Computing: Cloud-based CMMS solutions offer scalability and flexibility. Businesses can access their systems from anywhere, improving collaboration and accessibility. Furthermore, cloud solutions tend to reduce costs associated with hardware and software maintenance.
These emerging technologies represent significant advancements that can enhance productivity and efficiency in maintenance management.
Predictive Maintenance and AI
Predictive maintenance, powered by artificial intelligence, is one of the most compelling future trends in CMMS. This approach allows organizations to shift from a reactive maintenance strategy to a proactive one.
- Artificial Intelligence (AI): AI algorithms analyze historical data to predict when an equipment failure may occur. By identifying patterns and trends, businesses can schedule maintenance before failures happen. This minimizes disruptions and can lead to significant savings in repair costs and production losses.
- Data Analytics: The integration of data analytics into CMMS systems enhances decision-making. Organizations can make informed choices based on insight gleaned from vast amounts of operational data. This data-driven approach is pivotal for optimizing maintenance schedules and resource allocation.
"Predictive maintenance not only anticipates issues but transforms maintenance from an unseen burden to a structured advantage."
The adoption of predictive maintenance strategies leads to a focus on reliability and efficiency, which is crucial for small to medium-sized businesses reliant on operational effectiveness.
Finale and Recommendations
The conclusion and recommendations section of this article serves as a pivotal component in synthesizing the insights gained throughout the exploration of various CMMS systems. In the context of this analysis, it holds significant importance, as it distills complex information into actionable steps for small to medium-sized businesses, entrepreneurs, and IT professionals.
As companies increasingly rely on technology for operational efficiency, understanding the nuances of CMMS becomes essential for informed decision-making. Selecting the right system can directly impact maintenance efficiency, asset longevity, and overall productivity. Thus, this section not only summarizes the key findings but also provides practical advice on selecting a CMMS that aligns with specific organizational needs.
Summary of Key Insights
The analysis presented in previous sections reveals several critical insights about the top CMMS systems available today:
- Diverse Features: Each CMMS system presents a unique set of features tailored for different operational requirements, including asset management, work order management, and reporting.
- Implementation Considerations: The process of implementing a CMMS requires careful planning. Factors such as cost, user training, and integration with existing systems must be considered thoroughly.
- User Feedback: Real-world user feedback indicates varied experiences with CMMS systems. Careful review of case studies can guide potential users in anticipating challenges and optimizing their utilization of the software.
- Cost Variability: Pricing structures differ significantly among systems, impacting budget decisions for small and medium enterprises. Understanding the total cost of ownership is crucial for making sound financial choices.
In summary, while all systems offer valuable functionalities, the effectiveness of a CMMS hinges on how well it aligns with the companyโs specific goals and processes.
Final Thoughts on Choosing a CMMS
Choosing a CMMS is not merely a transactional decision; it is a strategic step that can influence the long-term operation of a business. Here are some recommendations to keep in mind:
- Assess Your Needs: Begin by evaluating your current maintenance practices. Identify weaknesses and areas for improvement. This assessment will inform your choice of features in a CMMS.
- Engage Stakeholders: Include all relevant parties in the decision-making process. Input from maintenance staff, IT professionals, and management can provide a holistic view of needs and preferences.
- Test Options: Take advantage of trials or demos offered by CMMS vendors. This hands-on approach will give insight into usability and compatibility with existing workflows.
- Look Ahead: Consider the scalability of the CMMS. As your business grows, your CMMS should adapt and grow accordingly.
The right choice of CMMS can empower businesses to streamline operations, increase asset reliability, and enhance maintenance strategies. This conclusion not only reinforces the significance of meticulously evaluating CMMS options but also encourages businesses to make prudent choices that align with their operational objectives.