Repairs Management Software: Key Insights and Comparison
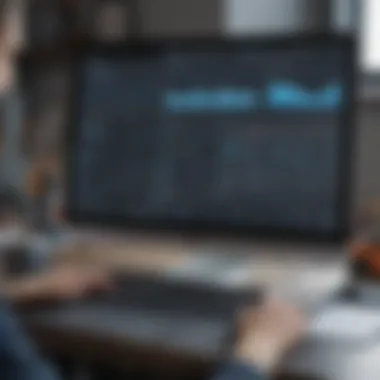
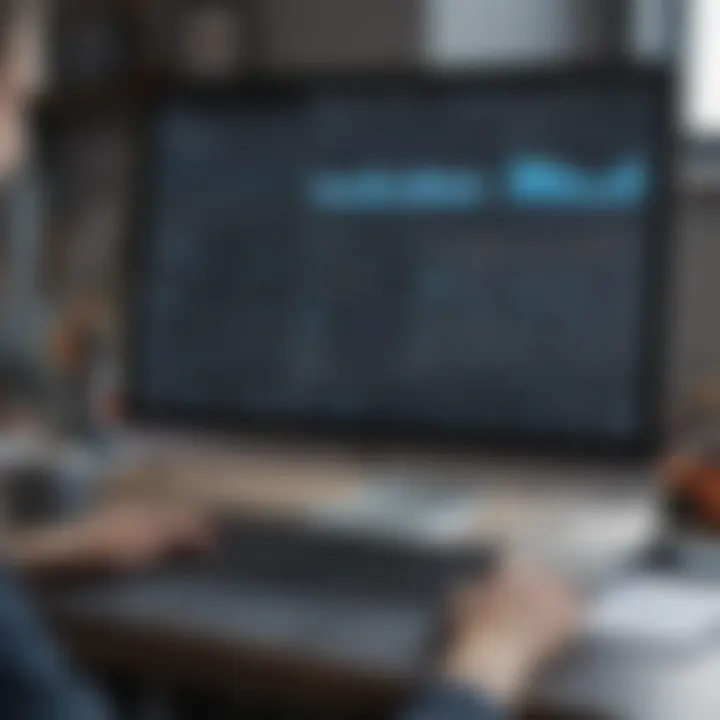
Intro
In the fast-paced world of modern business, where every minute counts, the importance of a streamlined repair process cannot be overstated. For small to medium-sized businesses, finding the right repairs management software can make the difference between a minor inconvenience and a major disruption. This software serves as a lifeline that connects various facets of repair management—from tracking requests to managing inventory and ensuring timely service delivery.
As we navigate through this comprehensive overview of repairs management software, we will explore its primary functions, essential features, and the broader landscape of competitors. It's essential to grasp how these tools can empower organizations, drive efficiency, and enhance productivity.
Software Overview
Definition and Purpose of the Software
Repairs management software is a specialized solution designed to assist businesses in managing all aspects of their repair processes. At its core, this software enables companies to organize their repair requests, schedule maintenance, allocate resources efficiently, and maintain comprehensive records of all repair activities. The purpose is not merely to fix things; it's about creating a robust framework that enhances operational efficiency.
Without such a system, businesses can find themselves bogged down by chaos—lost tickets, unhappy customers, and an endless back-and-forth between departments. The software is meant to automate and streamline these processes, freeing up valuable time for employees to focus on other critical tasks.
Key Features and Functionalities
When searching for the right repairs management software, certain features stand out as non-negotiable.
- Ticket Management: A centralized system that allows users to log repair requests, track status changes, and ensure each task is completed promptly.
- Scheduling Tools: Features that help in planning and scheduling repairs, assessing availability of staff, and managing workloads effectively.
- Inventory Tracking: Monitoring parts and materials in real-time ensures that the necessary resources are on hand when needed.
- Reporting and Analytics: Robust analytics tools provide insights into repair patterns, operational efficiency, and areas needing improvement, allowing for informed decision-making.
- User-Friendly Interface: A software might have all the right features, but if it's complicated to navigate, it defeats the purpose. A clean, intuitive interface enhances productivity.
These functionalities are crucial for businesses aiming to stay on top of their repair game and enhance customer satisfaction.
Comparison with Alternatives
Overview of Competitors in the Market
The repairs management software market is ever-growing, with numerous players vying for attention. Notable competitors include ServiceTitan, RepairShopr, and mHelpDesk, each offering unique functionalities tailored to meet diverse needs of businesses.
As repairs management evolves, these competitors have started to differentiate themselves through various innovative features, pricing models, or user experiences.
Key Differentiators
When comparing repairs management software solutions, it’s important to identify what sets them apart:
- Customization Options: Some platforms allow extensive customization to suit specific business needs, which can be a game changer for niche industries.
- Integration Capabilities: The ability to seamlessly integrate with existing systems—be it accounting software or customer relationship management tools—is vital for many businesses.
- Customer Support: Availability of comprehensive support and training to ensure users can maximize the software’s potential effectively.
- Mobile Access: With the growing trend of remote work and mobility, having a platform that offers robust mobile functionalities is increasingly important.
Each of these aspects can significantly impact a business's choice of repairs management software.
The goal isn't just to streamline repairs; it’s about creating a seamless workflow that enhances overall productivity.
As we continue through this overview, we will delve deeper into best practices for implementation and more tailored insights to aid stakeholders in making informed decisions.
Understanding Repairs Management Software
In the realm of business operations, repairs management software is becoming an indispensable tool, especially for small to medium-sized enterprises. Understanding this software goes beyond just knowing its features; it requires grasping its role in enhancing workflows, reducing overhead, and ensuring that repairs are managed efficiently. Whether you're a business owner or an IT professional, delving into the details of repairs management software offers insights into how it operates and the significant advantages it provides.
Primarily, repairs management software assists organizations in tracking the lifecycle of repair requests, streamlining the entire process from initiation to resolution. This includes everything from assigning tasks to technicians to tracking the materials used in repairs. When businesses implement this type of software, they witness an improvement in communication between departments and a reduction in response times. Such efficiency often translates to better service delivery, creating a more satisfied customer base.
Furthermore, as the market for this software continues to evolve, it’s essential to keep abreast of the latest trends and innovations. Knowing the historical context of repairs management software can provide clarity on its current capabilities and the expected trajectory. This knowledge equips decision-makers to leverage such tools for strategic advantages, enabling organizations to stay competitive in their respective industries.
Definition and Purpose
Repairs management software can be defined as a specialized tool designed to manage and streamline the repair processes within various sectors. Its purpose is multifaceted, which primarily hinges on improving the efficiency and effectiveness of repair operations. In essence, it acts as a centralized platform where all repair-related information is documented, tracked, and analyzed.
This software allows businesses to manage work orders effectively, track assets, maintain inventory, and generate reports that showcase operational performance. By automating these tasks, organizations can focus their resources more strategically, rather than getting bogged down by manual processes that are prone to errors.
Historical Context
The evolution of repairs management software can be traced back to the changing needs of businesses seeking better organization and efficiency. Initially, repair tracking was done through manual logs and spreadsheets, which, while functional, presented several challenges. Information could become lost, much time would be wasted in searching for the right data, and errors were often a common occurrence.
Over the years, technological advances have spurred the development of more sophisticated systems. This shift is mainly attributed to the rise of digital transformation and the advent of cloud-based services. In the 1990s and early 2000s, more manufacturers and service providers recognized the necessity of software solutions that cater specifically to repairs management. Today, we see tools that integrate with Internet of Things (IoT) technology, offering real-time tracking and analytics, which ultimately enhances decision-making processes.
As businesses adopt repairs management software, they not only streamline their operations but also pave the way for innovation and improved customer satisfaction.
Key Features of Repairs Management Software
Understanding the fundamental features of repairs management software is like having a sturdy foundation for a house—it keeps the whole structure sound. Each feature addresses specific needs within an organization, enhancing the overall functioning of repair processes. With the right tools, businesses can improve communication, ensure accountability, and ultimately provide better service to their clients. Let’s delve into the critical components that form the backbone of effective repairs management software.
Work Order Management
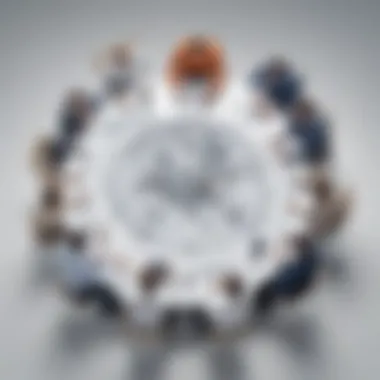
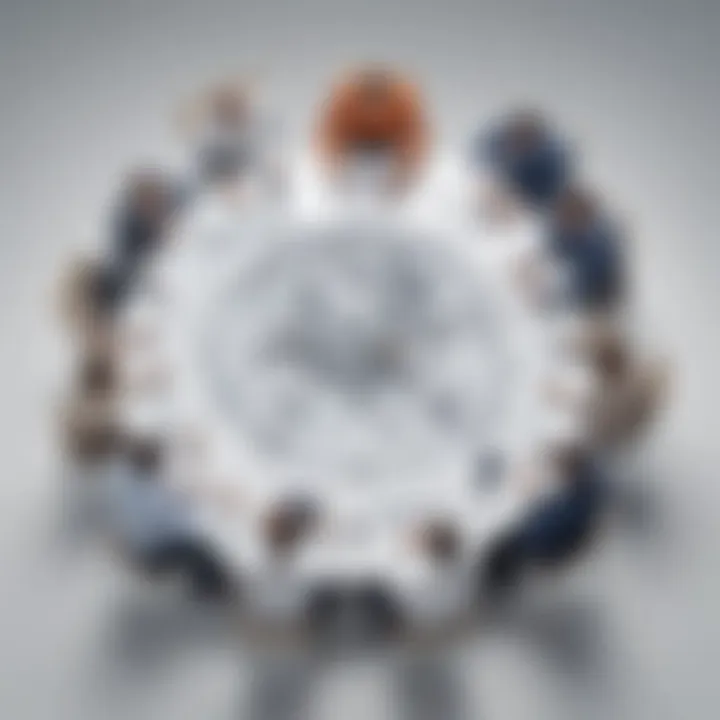
Work order management is at the heart of repairs management software. It streamlines the process of assigning tasks, scheduling jobs, and tracking progress. By creating a clear workflow, organizations can ensure that no task gets lost in the shuffle.
For instance, when a repair request comes in, a technician can quickly assess the urgency by looking at the assigned work orders. This feature not only organizes tasks but also allows managers to prioritize jobs based on availability and importance. As a result, businesses can reduce downtime and enhance customer satisfaction.
Here are the essential elements that work order management typically covers:
- Job Creation: Quickly convert service requests into work orders.
- Scheduling: Assign tasks based on staff availability or expertise.
- Tracking: Monitor the status in real-time, keeping all stakeholders in the loop.
- Completion: Ensure work is completed and clients are notified efficiently.
The impact of effective work order management cannot be overstated—as technology advances, so does the necessity for proactive task management that mitigates delays and errors.
Asset Tracking
Asset tracking is another pivotal aspect of repairs management software. Keeping a finger on the pulse of every asset’s whereabouts ensures that organizations maximize the utility of their resources. Typically, businesses lose a considerable amount of money on dormant equipment or misplaced tools.
Using advanced asset tracking functionalities, teams can:
- Monitor Location: Know exactly where each asset is located at all times.
- Maintain Maintenance History: Keep a detailed log of repairs and servicing to forecast future needs.
- Optimize Usage: Identify underutilized assets to better allocate resources.
Investing in solid asset tracking capabilities translates into better management decisions and reduces costs associated with lost or unused equipment. It’s one less thing to worry about when there’s clarity around resource usage.
Inventory Management
Inventory management is often an overlooked aspect of repairs management software, but it definitely deserves its roses. It helps ensure that technicians have the right parts on hand when they need them. When inventory levels are managed effectively, businesses can dodge the pitfalls of overstocking or stockouts.
Key points regarding inventory management features include:
- Real-time Stock Levels: Easily check what’s available and when new stock should arrive.
- Automated Reordering: Set thresholds to trigger orders automatically, ensuring continuous supply.
- Reporting: Generate reports that give insights into usage patterns and cost savings.
Good inventory management plays an essential role in increasing efficiency, ensuring that repairs can be carried out without unnecessary hindrances. Saving time here means more satisfied customers down the line.
Reporting and Analytics
The decision-making process becomes straightforward when repair data is presented effectively. This is where reporting and analytics come into play. By harnessing the power of data, businesses can uncover trends, measure performance, and inform strategic changes.
Some notable features of reporting and analytics include:
- Key Performance Indicators (KPIs): Track metrics like repair turnaround time and technician productivity, allowing managers to identify areas for improvement.
- Custom Reports: Generate tailored reports that resonate with specific operational needs.
- Visual Dashboards: Maintain a real-time overview of performance through intuitive visuals.
In a world where data drives decisions, effective reporting is a game-changer. It can transform a business from reactive to proactive, consequently improving the bottom line.
"Having the right features in repairs management software not just simplifies operations but also acts as a compass guiding businesses toward strategic decisions that lead to growth."
Benefits of Implementing Repairs Management Software
Repairs management software plays a crucial role in modern business operations. When properly rolled out, it streamlines workflows, cuts down on unnecessary costs, and enhances accuracy in tracking repairs. Focusing on the benefits can give organizations the competitive edge they need to flourish in a fast-paced environment. Let's delve into the key advantages such software brings to the table, ensuring that small and medium-sized enterprises as well as ambitious entrepreneurs can maximize their gains.
Increased Efficiency
One of the most noteworthy perks of repairs management software is the significant boost in efficiency it can offer. By automating various routine tasks, employees can focus on areas that require their expertise rather than being bogged down by mundane paperwork or manual tracking. For instance, one can set up automatic notifications for maintenance schedules, ensuring no equipment goes unchecked.
- Automation frees up time.
- Centralized information reduces search time for necessary data.
- Streamlined communication allows for quicker decision-making.
With an intuitive platform, team members can easily collaborate on work orders, share updates, and even access historical data to assess past repairs. The increased transparency keeps everyone on the same page and fosters accountability among staff.
"Efficiency isn't a goal; it's a way of life. Embracing repairs management software can make that life a whole lot easier."
Cost Reduction
Effective cost management is every business owner's dream, and repairs management software helps achieve just that. By eliminating redundancies and optimizing resource allocation, companies may identify areas where they were overspending. For example, with clearer insights into inventory levels, businesses can avoid purchasing excessive spare parts or managing an unproductive labor force.
Key cost-saving aspects include:
- Lower downtime due to timely repairs, leading to increased productivity.
- Reduced manual labor costs as processes get automated.
- Avoiding penalties and fines associated with non-compliance through organized record-keeping.
Implementing such software can also contribute to a longer lifespan for equipment, as proactive maintenance helps prevent costly breakdowns. When resources are used efficiently, the overall financial health of a business improves, creating more opportunities for growth.
Improved Accuracy
The precision provided by repairs management software cannot be understated. Human error is all too common when tracking repairs through manual processes, often resulting in costly mistakes. By shifting to a digital platform, organizations can enhance the precision of their operations in several ways.
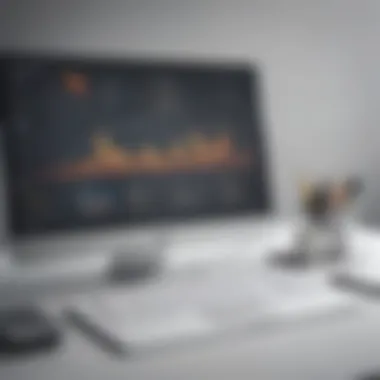
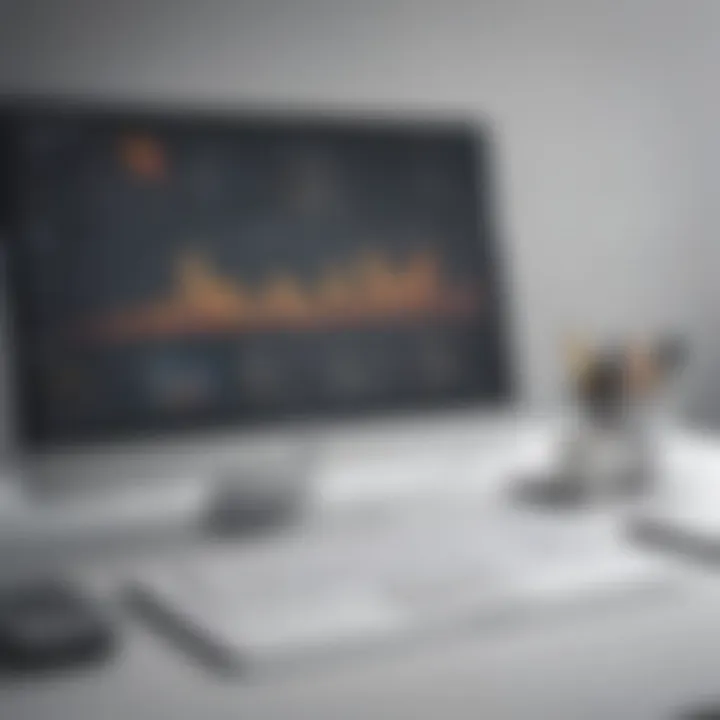
- All data is updated in real-time, reducing the chances of discrepancies.
- Automated reports minimize the risk of misreporting or overlooking essential details.
- Accurate inventory tracking helps avoid stockouts and overstocking incidents.
This improved accuracy can reinforce trust among stakeholders, as reliable record-keeping often leads to better relationships with clients and vendors alike. Organizations can adapt quickly to changes in demand, fulfilling orders with confidence that everything is correctly accounted for.
In summary, the benefits of implementing repairs management software are significant. From boosting efficiency to enabling cost reduction and enhancing accuracy, these advantages impact the bottom line. By embracing technology in their operations, businesses position themselves for lasting success in a competitive landscape.
Challenges of Repairs Management Software
While repairs management software is ultimately designed to streamline operations and enhance productivity, several challenges can impede effective implementation and utilization. Recognizing these challenges is critical for small to medium-sized businesses, entrepreneurs, and IT professionals. Understanding what lies beneath the surface can make the difference between a successful deployment and a costly failure. This section dives deep into the hurdles that organizations might face.
Implementation Issues
Implementing repairs management software can sometimes feel like trying to fit a square peg in a round hole. A common pitfall is misalignment between the software capabilities and the organization’s specific needs. For instance, a company might invest in high-end software that offers a plethora of features, but if those features do not resonate with their operational workflow, it can lead to confusion, frustration, and inefficiency.
Moreover, the technical setup can prove overwhelming. Integrating a new system often requires migrating existing data, which can be fraught with errors if not handled meticulously. A heck of a lot of planning is required to map out who will be responsible for what during this phase. Businesses often overlook the importance of having a carefully drafted implementation plan, leading to deadlines missed and resources wasted.
User Resistance
One significant barrier to the successful adoption of repairs management software is user resistance. It is human nature to be wary of changes, especially when individuals are comfortable with existing procedures. Employees may feel that their jobs are at risk if machines take over previous tasks or feel that incorporating new software is simply adding more complexity to their workday.
To combat this reticence, active involvement from all team members is essential during the selection and implementation phase. Training sessions and open forums for discussion can pave the way. Acknowledging the staff's concerns while demonstrating the benefits of the new software helps forge a positive experience. People often get on board when they can visualize how the software will work in their daily routines — when it focuses on improving their tasks and reducing their workload.
Maintenance Costs
Even after successfully integrating repairs management software, organizations must stay vigilant about ongoing maintenance costs. While the initial purchase may seem manageable, additional expenses can quickly add up. Licensing fees, regular updates, and technical support often chew through budgets like a beaver gnawing on wood.
Furthermore, as businesses evolve, they may uncover the need to upgrade or tweak their software to better align with new practices. This can lead to unexpected financial burdens, particularly for small businesses that might already be running on tight margins. A proactive approach in budgeting for these potential costs can help avoid the pitfall of overspending and misallocation of resources.
"Understanding the challenges is the first step to overcoming them. Ignoring potential pitfalls can lead to a costly misalignment with the organization’s goals."
In summary, while repairs management software presents significant advantages, recognizing and addressing the challenges associated with its implementation, user acceptance, and ongoing maintenance is essential for ensuring long-term success. Being prepared to tackle these issues not only improves the software's efficacy but also enhances the overall operational efficiency of a business.
Comparison of Leading Repairs Management Software Solutions
In a sea of choices, the task of picking the right repairs management software can feel like trying to find a needle in a haystack. Each option brings its own set of features, strengths, and weaknesses, making a thorough comparison essential. This section aims to illuminate the key criteria that businesses should consider while navigating through the landscape of repairs management solutions. Choosing the right software not only affects day-to-day operations but also contributes to long-term success and scalability. Understanding what each software brings to the table allows decision-makers to make informed choices that align closely with their organizational goals.
Overview of Market Leaders
When it comes to repairs management software, several names frequently pop up in discussions among small to medium-sized businesses. These include:
- FMX: Known for its user-friendly interface and strong work order management capabilities, FMX is a good fit for organizations focused on efficiency.
- Hippo CMMS: With robust customization options, Hippo is ideal for companies needing tailored solutions.
- Maintenance Connection: This platform excels in asset tracking and professional reporting, making it a staple for industries that rely on data.
Each of these platforms has carved out its niche, often catering to specific industries such as manufacturing, facilities management, or property management. As we delve deeper into the next sections, we will explore what distinguishes these leaders from one another.
Feature-by-Feature Comparison
A careful examination of features can often reveal whether a solution meets an organization’s unique requirements. Here are some vital features to consider when comparing repairs management software:
- Work Order Management: How does the software facilitate the creation, assignment, and tracking of work orders? Features like drag-and-drop functionality or quick-response templates can enhance the user's experience significantly.
- Asset Tracking: Does the software allow real-time updates on asset locations and conditions? This determines how effectively an organization can manage and maintain its resources.
- Reporting and Analytics: The ability to generate insightful reports is crucial. Look for options that provide customizable dashboards that align with KPIs relevant to your business.
"It's not just about what features a software has — it's about how those features integrate into your existing processes."
Cost Analysis
Cost is a big part of the decision-making process, and understanding pricing models will save both money and headaches down the line. Many solutions operate on subscription-based pricing, which can offer flexibility but also add up over time. Factors influencing the cost of repairs management software include:
- Initial Setup Costs: Some software may require significant upfront investment for installation and training.
- Monthly Subscription: Does the service charge per user, or is there a flat rate? This can greatly affect small businesses with tight budgets.
- Additional Fees: Always inquire about potential hidden fees for features like extra storage, advanced analytics, or additional user licenses.
By conducting a detailed cost analysis alongside feature comparisons, businesses gain a clearer picture and can better understand which solution fits their financial constraints while delivering the desired functionality.
Selecting the Right Repairs Management Software
Choosing the right repairs management software can feel like finding a needle in a haystack, especially with the myriad of options available today. This stage is crucial for any business, particularly small to medium-sized enterprises that might not have the luxury of an expansive IT budget. A sound choice does more than just streamline operations; it sets the foundation for overall organizational effectiveness. One misstep in selection can lead to a heap of frustrations, from wasted funds to loss of productivity. Thus, understanding how to navigate this decision-making process is of utmost importance.
Assessing Organizational Needs
Before diving into the sea of available options, it’s vital to conduct a thorough needs assessment. This is akin to measuring a room before purchasing furniture; without proper measurements, the pieces might not fit. Engage with your team to gather insights on what challenges they face and what features would aid in their daily responsibilities.
- Identify Core Functions: Determine what aspects of repairs management are critical for your organization. Is it primarily work order management, inventory control, or perhaps asset tracking?
- User Preferences: Different departments may have differing needs. What works for maintenance staff might not suit the accounting department. Make sure to understand specific user requirements.
- Growth Expectations: Think about where you want your business to be in a few years. Will you need software that scales? It’s better to choose a flexible solution now than to migrate later.
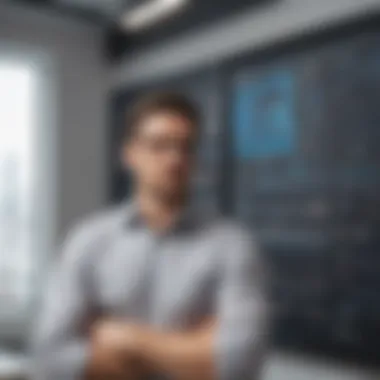
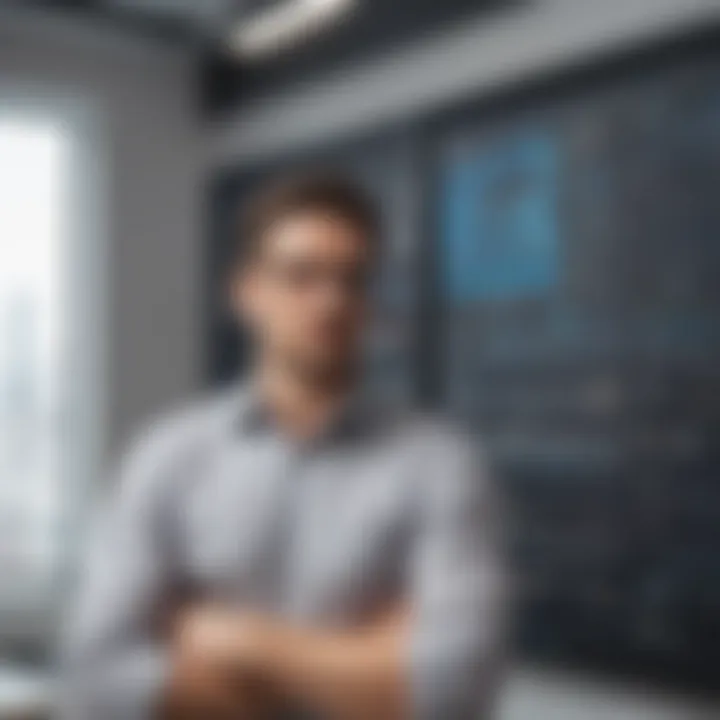
Evaluating Software Options
Once the needs are assessed, the next step is evaluating the software options available. With so many products on the market, distinguishing the wheat from the chaff is crucial.
- Feature Alignment: Compare the features of various software solutions against your organized needs assessment. Listings on software review sites are helpful, but cross-reference with direct competitor offerings to avoid any gaps.
- User Experience: A clunky user interface can be a significant barrier. Look for software that keeps usability on the forefront, ensuring that training time is minimized and adoption rates are maximized.
- Demonstration and Trials: Engage with vendors for demo versions. This hands-on approach will help you gauge how the software performs in real-world conditions. A trial period can reveal a lot more about user experience than a polished marketing brochure ever will.
Vendor Support and Training
The right software can only be as good as the support that comes with it. When selecting repairs management software, scrutinizing the vendor’s support structure is essential. This can be the difference between a seamless implementation and prolonged headaches.
- Support Accessibility: Confirm that the vendor offers reliable customer support. During critical periods, being able to reach a knowledgeable representative is invaluable.
- Training Resources: Look at how comprehensive the vendor’s training program is. Could it be through on-site training, webinars, or manuals? The more resources available can significantly ease the onboarding process.
- Feedback Mechanism: Ensure that the provider values feedback. This fosters a long-term relationship and facilitates continuous improvement of current functionalities based on actual user experience.
"The decision you make today about repairs management software can shape your operational efficiency tomorrow."
Making an informed choice based on solid assessments and evaluations aids not only in daily management but ensures a future-proof setup, allowing you to focus on what really matters: growing your business.
Best Practices for Implementation
Implementing repairs management software can be a real game changer for small to medium-sized businesses looking to enhance their operational efficiency. However, a successful implementation doesn't just land in your lap; it requires careful planning and dedicated resources. Following some best practices can make the transition smoother and maximize the potential benefits. It's not just about adopting a tool; it's about integrating it into the very fabric of your operations. Here’s a deep dive into making that happen effectively.
Creating a Clear Implementation Plan
The backbone of any successful software implementation is a well-defined plan. Think of it as assembling furniture from a kit—if you don’t have clear instructions, you might end up with leftover screws and a wobbly chair. Start by outlining your objectives; what do you hope to accomplish with the new software? Is it increased response time on repairs, better tracking of assets, or perhaps a more streamlined communication process?
It’s crucial to break these objectives down into measurable milestones. Engage your team in this process, as their insights will come in handy. List out tasks, assign responsibilities, and set realistic timelines. This will not only prevent chaos but also hold everyone accountable along the way.
Remember, a good implementation plan is akin to a roadmap. You don’t just want to know where you’re headed, but how you aim to get there.
Involving Key Stakeholders
Often, businesses overlook the importance of involving key stakeholders during the implementation phase. These stakeholders could range from department heads and IT personnel to front-line workers who will ultimately use the software daily. Their involvement is essential for a few reasons.
First, you gather diverse perspectives—each stakeholder will have unique insights into the needs and challenges of their respective areas. Their input can highlight potential pitfalls and unique requirements that you might have missed.
Second, it fosters a sense of ownership. When stakeholders feel they have a say in the implementation process, they're more likely to embrace the change. Arrange regular meetings, updates, and feedback sessions. You want to ensure everyone is in the loop and that they feel they’re part of the solution, not just the recipients of it.
“Collaboration is the glue that holds a successful implementation together.”
Continuous Training and Support
Investing in software is just the beginning; ensuring your team knows how to use it efficiently is where the magic happens. Continuous training and support can’t be a one-off workshop. Like learning to ride a bike, it takes practice and sometimes a nudge when someone wobbles.
Consider establishing a training schedule that allows employees to continuously improve their skills with the software. This could be through periodic workshops, online tutorials, or even one-on-one sessions with a dedicated support team. Further, ensure that there’s always a point of contact for any queries or issues that arise post-implementation.
Regularly updating training materials and support can help users adapt to software updates or feature enhancements as they roll out.
Future Trends in Repairs Management Software
As the commercial landscape continues to shift beneath us, one cannot overlook the rising trends shaping repairs management software. It's no longer just about managing workflows; it’s about incorporating innovative technologies that transform how businesses operate internally and interact with clients. Keeping an eye on these trends is crucial for organizations that wish to maintain a competitive edge and ensure their repair processes are as streamlined as possible.
Integration with IoT
The Internet of Things (IoT) is transforming various industries, and repairs management is no exception. IoT-enabled devices can provide real-time data feeds, allowing managers to monitor assets and equipment status remotely. Imagine a situation where a predictive signal from a machine indicates that a part may fail soon. With IoT integration, maintenance requirements can be identified before they evolve into costly breakdowns.
Moreover, integrating IoT can help automate the work order process. When an issue arises, the IoT device can automatically generate a work order, ensuring that repair teams are notified immediately. This reduces response time, allowing businesses to operate efficiently. As machines become smarter, the need for software to handle these streams of data becomes paramount. It's a leap towards preventive maintenance over reactive measures, ultimately saving time and increasing productivity.
AI and Predictive Maintenance
Artificial intelligence (AI) introduced a new level of sophistication to repairs management software. Predictive maintenance, powered by AI, utilizes algorithms to analyze data from various sources like IoT devices and historical records. The aim is to predict when equipment or machinery will fail, allowing maintenance to be scheduled at optimal times.
The benefits of AI in predictive maintenance extend beyond mere scheduling. By analyzing patterns and anomalies, AI can help organizations understand wear and tear better than traditional methods. They can anticipate failures more accurately and allocate resources wisely. This means lesser money sunk into last-minute repairs, and it also extends the life of equipment.
The real kicker? This predictive capability allows small to medium-sized businesses to plan their budgets around maintenance needs, making it cheaper and more efficient in the long run. As AI evolves, expect repairs management software to become even more intuitive and useful.
Cloud-Based Solutions
Cloud computing represents a significant shift in how repairs management software is delivered and accessed. Traditionally, businesses operated on local servers, which required hefty investments for maintenance and upgrades. However, cloud-based solutions eliminate these barriers, allowing businesses to access the software from almost anywhere.
The flexibility offered by cloud computing also promotes collaboration among team members. Multiple users can access data in real time, leading to enhanced communication and quicker decision-making. Furthermore, cloud-based solutions often provide a pay-per-use option, which is incredibly appealing for small businesses looking to manage costs effectively.
Security, often a concern with cloud systems, has improved significantly. Many providers now offer robust security features that protect sensitive data. This enables businesses to leverage the benefits of technology without compromising on safety.
"Organizations that align their operations with technological advancements are often the ones that thrive in competitive landscapes."
As the field of repairs management software continues to mature, the future undoubtedly holds exciting possibilities, inviting businesses to lean into innovation for survival and growth.