Software Solutions for PCB Design: A Detailed Review
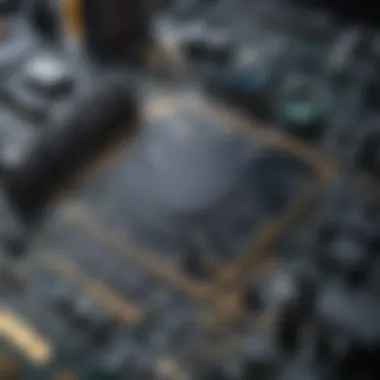
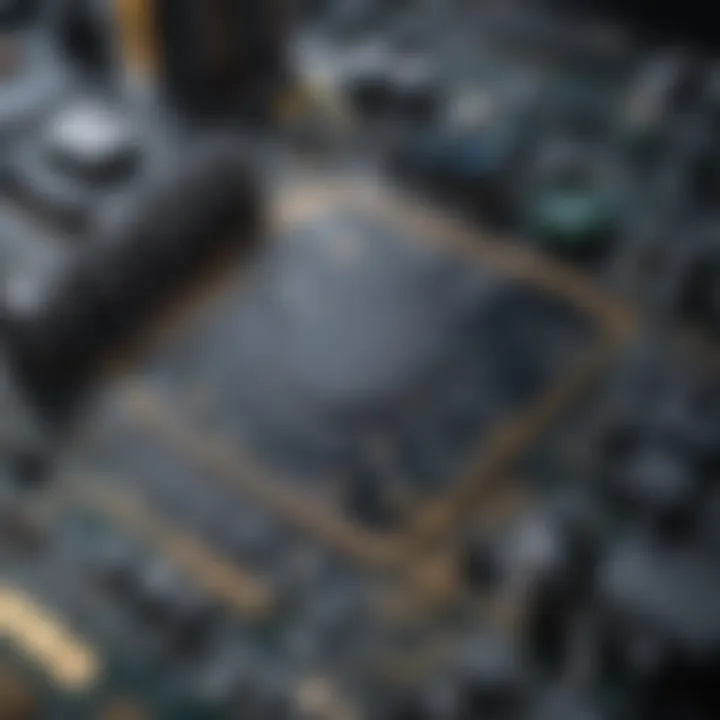
Intro
In today's tech-driven world, the demand for printed circuit boards (PCBs) continues to grow. These are essential for various electronic devices, from smartphones to industrial machinery. Consequently, the software tools used for PCB design have become critical components in ensuring efficiency and accuracy in the design process. This article explores the range of software solutions available, focusing on their functionalities and how they cater to the diverse needs of businesses.
Software Overview
Definition and Purpose of the Software
PCB design software enables engineers and designers to create circuit layouts efficiently. The primary purpose of these tools is to simplify the process of designing, prototyping, and producing PCBs. Such software often incorporates simulation capabilities to test the circuit's functionality before physical production, reducing errors and material costs.
Key Features and Functionalities
PCB design software comes equipped with several key features:
- Schematic Capture: This allows users to create, edit, and manage circuit schematics clearly.
- Layout Tools: Users can translate their schematics into physical layouts that define how components will be arranged on the board.
- Design Rule Check: This feature automatically checks for any errors or inconsistencies in design before production.
- 3D Visualization: Many modern software solutions offer 3D views of the PCB, enabling designers to visualize the layout and components in a spatial context.
- Export Options: The ability to export designs in various formats is crucial for collaboration and sharing with manufacturers.
These features collectively aim to enhance the designer's workflow, ensuring that PCBs are not only functional but also optimized for performance.
Comparison with Alternatives
Overview of Competitors in the Market
The market for PCB design software includes both well-established names and emerging competitors. Notable software options include Altium Designer, Eagle PCB, KiCAD, and OrCAD. Each software suite has its unique strengths that cater to different aspects of PCB design.
Key Differentiators
When comparing these tools, certain aspects set them apart:
- User Interface: Altium Designer is known for its intuitive interface, while KiCAD often appeals to users seeking open-source solutions.
- Pricing: Eagle PCB offers flexible pricing options, making it a popular choice among small to medium-sized businesses.
- Community and Support: KiCAD, being open-source, has a vibrant community that offers support and shared resources.
Understanding these differentiators can assist professionals in selecting the right tool that aligns with their specific project requirements and budget.
Understanding PCB Design
In the realm of electronics, PCB design underscores a pivotal process that directly influences the performance and reliability of electronic devices. Printed Circuit Boards, or PCBs, serve as the backbone of electronic hardware, facilitating connections between different components such as resistors, capacitors, and integrated circuits. As technology evolves, the complexity of PCB design has increased, necessitating sophisticated tools and methodologies to create efficient layouts. Understanding PCB design is essential for engineers, designers, and even entrepreneurs in the electronics sector, as it sets the framework for creating high-quality products that meet user needs and regulatory standards.
A clear grasp of PCB design fundamentals allows professionals to visualize how electronic devices will function. It ensures that signals pass without interference and that components fit well together, maximizing the use of space and minimizing errors. Addressing these elements effectively leads to higher reliability, extends product life cycles, and ultimately results in customer satisfaction.
Fundamentals of PCB Design
At its core, PCB design involves several fundamental elements β material selection, layer stacking, schematic capture, and layout design are all critical parts of the process. Each element plays a significant role in ensuring that the final product meets the intended electrical specifications and functions as required.
- Material Selection: The choice of material affects not only the physical properties of the board but also its performance regarding heat dissipation and electrical conductivity. Common materials include FR-4 for its excellent balance between cost and performance.
- Layer Stacking: Determining how many layers a PCB requires is crucial. Multi-layered boards can accommodate complex designs with more components while ensuring proper routing.
- Schematic Capture: This step involves creating a symbolic representation of the circuit. It serves as a blueprint for the design, detailing connections among components and providing a clear understanding of the circuit's operation.
- Layout Design: This final phase arranges components on the board and establishes traces that connect them. Effective layout design minimizes signal interference and optimizes space within the board.
Understanding these fundamentals is paramount to successful PCB design, as each aspect impacts the performance of the electronic device.
Importance of Software in PCB Design
Software plays an instrumental role in facilitating modern PCB design. Given the complexity of circuits and the need for precision, specialized software addresses various design requirements. The right PCB design software enhances efficiency, reduces human errors, and offers simulation capabilities that traditional methods cannot match.
Using software, designers can:
- Visualize Designs: Softwares provide a graphical interface for visualizing board layouts, enabling quick adjustments and a clear overview of the design.
- Run Simulations: Before physical production, simulations can identify potential design flaws. This proactive approach saves time and resources.
- Streamline Collaboration: Many platforms support team collaboration, allowing multiple stakeholders to contribute to or review designs in real time.
- Generate Documentation: Effective software streamlines the creation of detailed documentation necessary for manufacturing and compliance.
"Effective PCB design software can be the difference between a successful product launch and costly design drawbacks."
Types of PCB Design Software
Understanding the different types of PCB design software is crucial in todayβs fast-paced technology environment. Each type of software serves a distinct purpose in the design process, contributing to efficiency, accuracy, and overall project success. Choosing the right software can make a substantial difference in how quickly and effectively a design can be executed. Small to medium-sized businesses, entrepreneurs, and IT professionals must consider various software types to meet their unique requirements and streamline their design workflows.
Schematic Capture Software
Schematic capture software is a fundamental component in PCB design. This type of software enables designers to create and edit schematic diagrams, which serve as the blueprint for the electronic circuit. The schematic typically includes symbols representing components and lines indicating connections between them.
The importance of schematic capture lies in its ability to translate complex ideas into a visual format that is easier to understand. These tools often provide libraries of components, making it simpler to find and use standardized parts in a design.
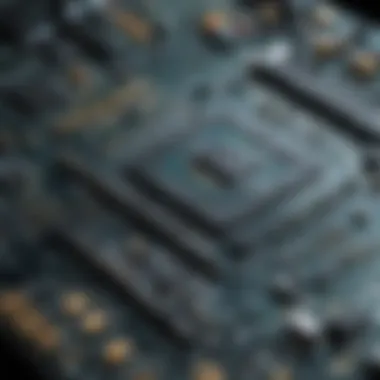
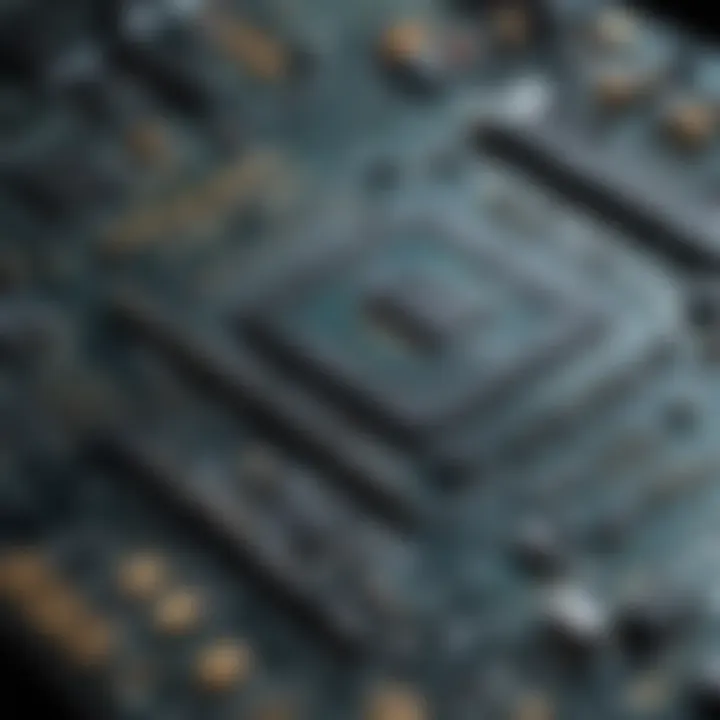
Some key benefits of schematic capture software include:
- Visualization: Provides a clear visual representation of the circuit, helping to identify errors early in the design process.
- Error Checking: Many software programs offer automated tools for checking connections and components, reducing the likelihood of design mistakes.
- Documentation: Generates documentation that assists during manufacturing and troubleshooting phases.
Popular tools in this category include Altium Designer and Eagle PCB, which allow designers to realize their visions through powerful schematic capture functionalities.
Layout Design Software
Layout design software is where the schematic comes to life. Once the schematic is completed, layout software is used to arrange the components as they will appear on the PCB. This involves placing components, routing connections, and optimizing the boardβs area.
The layout phase is critical, as it influences the board's performance, manufacturability, and thermal characteristics. An intuitive layout design tool will facilitate efficient placement and routing, contributing to a more streamlined design process.
Some notable aspects of layout design software include:
- Routing Capabilities: Advanced routing features help in connecting components efficiently.
- Design Rule Check (DRC): Ensures the layout adheres to manufacturing specifications, avoiding potential issues down the line.
- 3D Visualization: Some tools allow designers to view the PCB in three dimensions, providing deeper insights into spatial relationships.
Simulation Software
Simulation software is essential for verifying the behavior of the designed PCB before actual production. These tools allow designers to test electrical characteristics, ensuring the circuit functions as intended.
Simulation helps in identifying potential problems that could arise during real-world usage. By simulating various conditions, designers can make necessary adjustments without the need for physical prototypes.
Key features of simulation software include:
- Performance Analysis: Enables creators to analyze the performance of circuits under different scenarios and conditions.
- Cost-Efficiency: Reduces the need for physical revisions by identifying issues in the software phase.
- Integration: Many simulation tools integrate seamlessly with schematic and layout software, streamlining the workflow.
In summary, selecting suitable PCB design software in these categories can significantly influence the design pipeline. It enables teams to work cohesively, reduces errors, and enhances project delivery timelines.
Key Features to Consider
When selecting software for printed circuit board (PCB) design, understanding key features is crucial. Various tools come with unique functionalities, each impacting the design workflow. Evaluating specific elements ensures that the software aligns with the user's needs and optimizes productivity. Considerations such as the user interface, integration capabilities, and overall cost structure can significantly influence the efficiency of the design process and the satisfaction of the user.
User Interface and Usability
A well-designed user interface (UI) is essential for any PCB design software. A clean, intuitive layout makes it easier for users to navigate through various functions. This is particularly important for small to medium-sized businesses that may not have extensive technical staff. Software with a complicated interface might slow down the learning process, leading to frustration.
Usability goes beyond aesthetics; it encompasses how effectively users can accomplish their tasks. Features like customizable toolbars, keyboard shortcuts, and straightforward navigation can enhance user experience. For example, Altium Designer features customizable menus and a robust drag-and-drop interface, allowing users to work more efficiently. This enables designers to focus on creativity instead of struggling with software complexities.
Integration with Other Tools
Integration with other tools can markedly improve the PCB design process. A software that works well with simulation programs, version control systems, and manufacturing tools can streamline workflows considerably. This holistic approach ensures that all stages of the design process are interconnected, which can reduce errors and enhance overall productivity.
For instance, tools such as KiCad allow for integration with external libraries and tools. This means that designers can adapt and enhance their schematics or layouts without having to switch environments constantly. Integration not only saves time but also optimizes the collaborative aspect of PCB design, making it easier for teams to work together effectively.
Cost and Licensing Structures
Cost is often a defining factor when selecting PCB design software, especially for small businesses or entrepreneurs. Various licensing structures exist β some tools offer one-time licenses, while others provide subscription models. Understanding the long-term costs associated with each option is essential for making an informed decision.
For example, Eagle PCB provides affordable subscription plans which can be appealing for startups. On the other hand, more advanced tools like OrCAD may require a significant initial investment but offer robust features that justify the cost. Businesses must evaluate their budgets against their project requirements to find a balance that meets both needs.
Selecting the right PCB design softwarerequires balancing usability, integration capabilities, and cost. Prioritizing these key features can lead to better design outcomes and efficiency in the PCB design process.
Popular PCB Design Software Solutions
In the realm of PCB design, selecting the right software solution is a pivotal decision for professionals. The wide array of available tools can significantly impact the efficiency, quality, and scalability of the design process. Opting for suitable software not only enhances productivity but also ensures that designs meet the required standards. Professionals, especially in small to medium-sized businesses, need to leverage these specialized tools for optimal results.
Various PCB design software solutions cater to different industry needs. Each option comes with its own set of features, strengths, and weaknesses. By understanding these, businesses can make informed choices that align with their specific project requirements and future growth plans.
Altium Designer
Altium Designer is a prominent choice for many PCB designers. Its integrated design environment combines schematic capture, PCB layout, and visual project management into a single platform. This coherence facilitates a smoother workflow, enabling users to model complex systems without switching between disparate tools.
One of its notable features is the advanced routing capabilities. Altiumβs interactive routing tools optimize signal integrity and reduce design cycles. Additionally, the software supports 3D visualization, allowing designers to see how components fit together, which is crucial for complex layouts. However, its cost can be a barrier for smaller enterprises.
Eagle PCB
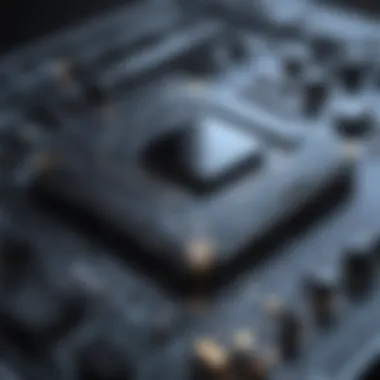
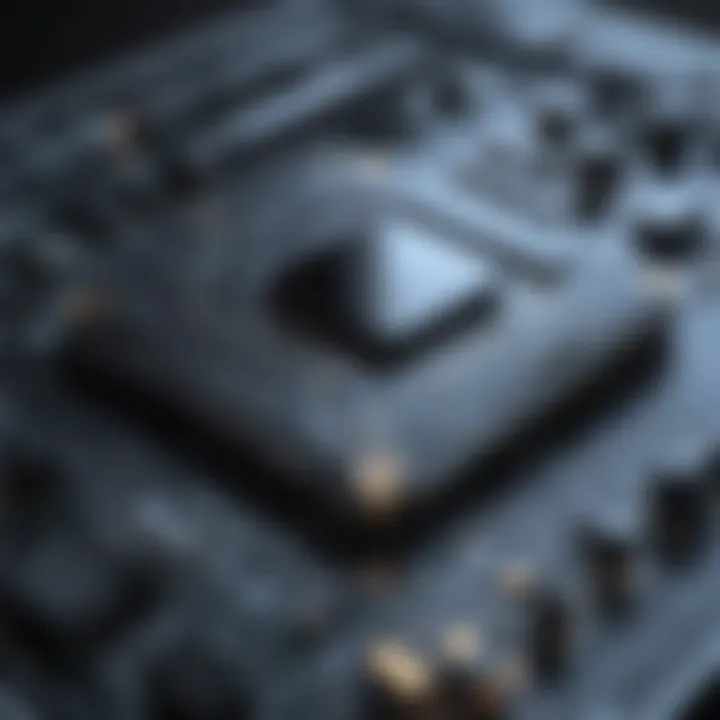
Eagle PCB, developed by Autodesk, is well-regarded among hobbyists and small businesses. It offers a user-friendly interface and a strong community support network. Its core features include schematic capture, PCB layout editing, and a library for components, making it a comprehensive tool for basic to intermediate designs.
A noticeable advantage is Eagleβs flexible licensing model. Users can access a free version with limitations, making it suitable for beginners. The software also integrates well with Autodeskβs other design tools, enhancing usability. Still, some advanced features found in competitors like Altium are lacking, which may limit its effectiveness for high-complexity projects.
KiCad
KiCad is an open-source PCB design software that has gained traction in recent years. It offers a suite of tools for schematic capture and PCB layout along with an extensive library of components. Being free of charge makes it an attractive option for startups and education sectors.
Despite its no-cost advantage, KiCad provides robust features, such as support for multi-layer PCBs and 3D viewer functionality. Moreover, it allows for extensive customization. However, the user interface may not be as polished as commercial alternatives, possibly making the learning curve a bit steeper for newcomers.
OrCAD
OrCAD, developed by Cadence Design Systems, is a powerful suite designed for professional PCB design. It excels in simulation tools that enhance the design verification process. OrCAD provides comprehensive support for both analog and digital designs, which makes it suitable for a broad spectrum of applications.
Its flexible licensing options also cater to various business needs. While it boasts a rich set of features, the complexity of the software can be overwhelming for new users. Those who invest the time to learn it, however, will find it to be a compelling tool for their design projects, particularly in sectors that require rigorous compliance and validation.
Emerging Trends in PCB Design Software
The landscape of PCB design software is constantly evolving. As technology advances, new trends emerge that significantly transform the approaches professionals take in designing printed circuit boards. Understanding these trends is crucial for small to medium-sized businesses and entrepreneurs looking to remain competitive in the market. Embracing these trends can lead to improved efficiency, better collaboration, and enhanced capabilities in PCB design.
Cloud-Based PCB Design
Cloud-based PCB design tools are gaining traction among engineers and designers. The primary advantage these tools bring is accessibility; users can access their projects from any device with internet connectivity. This flexibility is particularly advantageous for teams who work remotely or are distributed across multiple locations.
One significant benefit of cloud-based solutions is collaboration. Teams can work on the same project simultaneously, allowing for real-time updates and changes. This co-working aspect reduces the chances of errors that occur when consolidating work from different team members. Moreover, cloud-based software often comes with automatic backups and version controls, reducing the risk of data loss.
Key factors to consider when selecting a cloud-based PCB design solution include:
- Security features: Since sensitive designs are stored online, robust security mechanisms are essential.
- Integration capabilities: Ensure that the software can integrate with existing tools and workflows seamlessly.
- Scalability: As your project requirements grow, the cloud solution should accommodate increased complexity without a hitch.
Collaboration Tools and Features
The future of PCB design is heavily focused on collaboration. With teams often spread across various locations, features that facilitate communication and teamwork are more important than ever. Modern PCB design software increasingly incorporates tools that enhance collaboration.
These tools may include chat functions, project management features, and integrated design review systems. Such collaboration features help keep all stakeholders informed, involved, and engaged throughout the design process.
Examples of effective collaboration functionalities are:
- Commenting and Annotations: Team members can leave comments directly on design files, facilitating discussions at specific points of interest.
- Integrated Meeting Tools: Some PCB design platforms even allow video conferencing or messaging to discuss designs and resolve queries in real time.
- Workflow Automation: These features automate routine tasks, allowing designers to focus on complex problems while ensuring all team members are on the same page.
In summary, embracing cloud-based solutions and collaboration tools can significantly enhance the PCB design process. By understanding and implementing these emerging trends, businesses can leverage technology to improve design efficiency and foster teamwork across projects.
Challenges in PCB Design
The process of printed circuit board (PCB) design is inherently complex, requiring a balance of technical skill, creativity, and rigorous attention to detail. In today's rapid-paced technology landscape, it is essential to recognize the challenges that can arise during PCB design. Identifying these obstacles is important because they can significantly impact the success of a product. Understanding the common pitfalls and manufacturing issues helps professionals create robust designs that are ready for market.
Common Design Errors
Errors in PCB design can lead to costly mistakes during production and can affect the functionality of the product. Common design errors include:
- Schematic mistakes: Misplaced components or incorrect connections in the schematic lead to dysfunctional circuits. It can be as simple as a missing connection or an overlooked component.
- Layout issues: Problems in the physical layout, such as poor component placement or inadequate trace widths, might result in overheating or signal integrity issues. Users must pay attention to the positioning of components to minimize interference.
- Design rule violations: PCB design software usually includes rules and constraints to prevent errors. Ignoring these rules can lead to component overlap, violations of spacing requirements, or other critical issues.
- Overlooking thermal management: Failing to consider heat dissipation can result in circuit failure. Proper design should incorporate heat sinks, thermal vias, and appropriate placement of heat-sensitive components.
- Test point considerations: Neglecting to designate test points can complicate troubleshooting efforts. Including strategic test points enables easier access during validation and debugging.
To mitigate these errors, designers should implement thorough review processes, employing both automated design rule checks and peer reviews.
Integration with Manufacturing
Integration with manufacturing is another vital challenge in PCB design. A poor understanding of manufacturing processes, such as fabrication and assembly, can lead to designs that are difficult or impossible to produce efficiently. Some key considerations include:
- Material selection: The choice of materials plays a significant role in manufacturability. Selecting materials that are compatible with the chosen processes can prevent delays and additional costs.
- Design for manufacturability (DFM): Designers must create PCBs with manufacturing capabilities in mind. This includes understanding assembly processes and ensuring that designs can be manufactured without significant rework.
- Communication with manufacturers: Establishing a strong collaboration with manufacturing partners is essential. Early involvement of manufacturers can help address potential issues before they arise, allowing for a smoother production cycle.
- Prototyping: Engaging in prototyping early in the design phase aids in identifying potential manufacturing challenges. Testing a physical prototype can highlight issues that might not be apparent in the design software.
Recognizing and addressing these challenges within the PCB design process ultimately ensures that the final product is not only functional but also manufacturable. By focusing on common design errors and integrating closely with manufacturing processes, businesses can significantly enhance their chances of success in a competitive market.
Best Practices for PCB Design Software Implementation
Implementing PCB design software effectively is crucial for small to medium-sized businesses and IT professionals. Best practices can significantly enhance productivity, streamline processes, and ensure high-quality designs. Concentrating on strategic implementation can lead to better outcomes and reduce errors in the workflow.
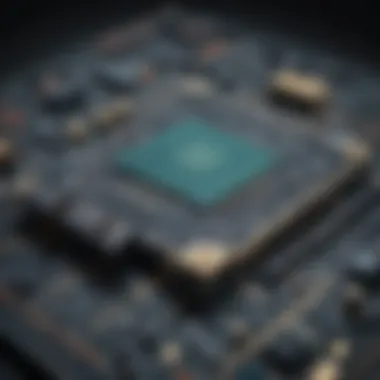
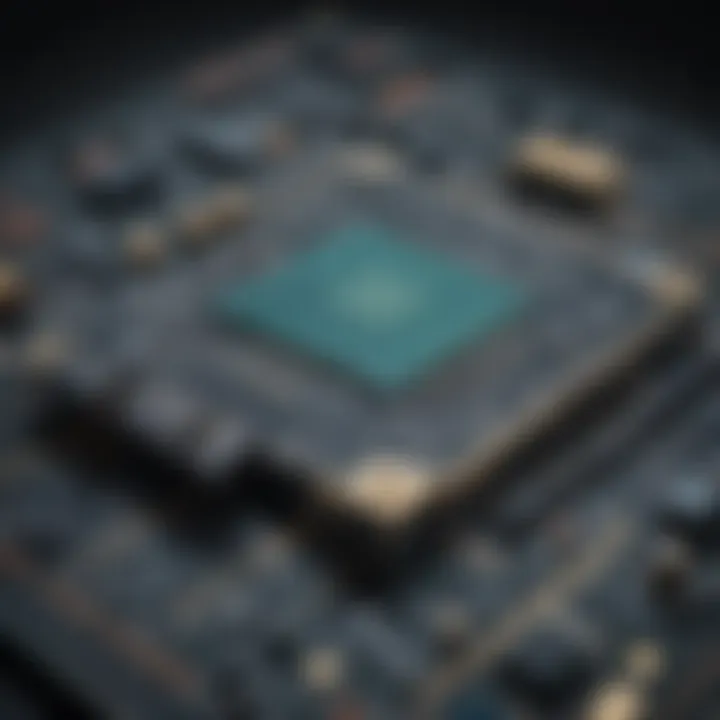
Training and Support
Training is an important aspect of using any software, especially in PCB design. Familiarizing team members with the software's functionalities can lead to better usage and increased efficiency. Proper training helps to decrease learning curves and set a foundation for productive usage.
Available training options vary from formal classes to online tutorials and vendor-led sessions.
- Formal Training: Often conducted by the software vendor, focuses on system features.
- Online Tutorials: Self-paced and cost-effective; ideal for continuous learning.
- Ongoing Support: Ensures that users can resolve any software-related issues that may arise post-deployment.
Such support minimizes disruptions in the design process and enhances the ability to troubleshoot issues quickly.
Proper training is essential to making the best use of PCB design software. It cannot be overlooked.
Version Control and Documentation
Version control and proper documentation are essential in PCB design, especially when multiple team members are involved. As designs evolve, maintaining clear records is vital to avoid confusion.
Establishing a version control system reinforces the integrity of designs. This process ensures that all changes are tracked and can be reverted if necessary. A few crucial practices include:
- Consistent Naming Conventions: Maintain clarity across different versions by using descriptive names.
- Regular Backups: Ensure that designs are backed up after significant changes to prevent data loss.
- Change Logs: Document any modifications with dates and details about the adjustments.
Documentation not only aids in recovery but also provides a reference point for future projects. Businesses can leverage well-structured documentation to onboard new team members and align team efforts quickly.
By incorporating training, support, and rigorous version control, teams can effectively implement PCB design software, enhancing their design process while minimizing potential risks.
Evaluating Software for Your Needs
In the realm of PCB design, selecting the right software is paramount. This choice can significantly impact your design efficiency, accuracy, and ultimately the success of the final product. Evaluating software for your needs involves understanding not only the features offered but also how these features align with your specific requirements. This section will examine the key considerations and benefits of a thorough evaluation process.
Identifying Specific Requirements
Before diving into the world of PCB design software, professionals must first delineate their specific needs. This requires a clear understanding of the overall project goals, team capabilities, and the technical specifications involved in the design process. Considerations may include:
- Complexity of Designs: Are you working on simple or complex designs? Higher complexity might necessitate advanced features.
- Collaboration Needs: Will multiple team members need to work on the design simultaneously? If so, integrated collaboration tools become essential.
- Integrated Testing: Determine if there's a need for simulation and testing features to validate designs before manufacturing.
- Budget Constraints: Understanding the budget helps narrow down choices. Different software offers various pricing structures that cater to different financial situations.
A well-defined set of requirements can guide your software selection, ensuring that you choose a tool that complements your teamβs workflow and project demands.
Conducting Software Trials
Once youβve identified your specific requirements, the next logical step is conducting software trials. Many software providers offer trial versions or demos which can be invaluable for testing the usability and fit for your needs. This phase should involve:
- Testing Usability: Assess how user-friendly the interface is. A steep learning curve can delay project timelines.
- Evaluating Performance: Check how the software handles your design requirements under real-world conditions. Performance indicators can include processing speed, responsiveness, and resource usage.
- Feedback from Team Members: Collect insights from the team who will ultimately be using the software. They can provide feedback that reflects practical usability and efficiency.
Engaging in software trials not only reveals the strengths of a program but also highlights potential limitations. Understanding these factors will empower you to make an informed decision, aligning software capabilities with project expectations.
Engaging in trials is essential. It provides a practical viewpoint that documentation cannot replace.
By effectively evaluating software against defined requirements and testing functionality through trials, businesses can minimize risks related to poor software fitment. This avoids future complications and enhances productivity in PCB design.
Closure
The conclusion of this article signifies a critical stage in understanding PCB design software. It encapsulates the breadth of information covered in previous sections, allowing readers to appreciate how each aspect contributes to choosing the right tool.
After exploring various software solutions, their features, and emerging trends, it becomes evident that selecting appropriate PCB design software is not just about functionality. It is about aligning that functionality with specific business needs. Small to medium-sized businesses and entrepreneurs, in particular, face unique challenges in PCB design that require thoughtful consideration of the software's usability, costs, and integration capabilities.
"Selecting PCB design software is a strategic decision that impacts overall design efficiency and product quality."
A key takeaway from this article is the recognition of the significance of training and version control in software implementation. Both elements directly affect how effectively a team can utilize the selected tool. Thus, as businesses transition to using new software, investing in adequate training and careful documentation becomes essential.
Additionally, businesses must stay attuned to future trends, such as cloud-based solutions and collaboration tools. These developments can greatly enhance workflow and ensure that teams remain agile in a dynamic technological landscape. Properly evaluating software against an organizationβs evolving needs will ensure long-term success and adaptability in PCB design processes.
Summary of Key Points
In summary, several essential points emerge from the discussion:
- Variety of Software Solutions: The landscape of PCB design software is diverse, offering options like Altium Designer, Eagle PCB, KiCad, and OrCAD. Each has its advantages and drawbacks, catering to different user requirements.
- Critical Features: User interface, integration capabilities, and licenses are paramount. Professionals should prioritize ease of use and compatibility with existing tools when selecting software.
- Emerging Trends: Keeping an eye on cloud-based solutions and collaboration features can significantly affect productivity and team dynamics in PCB design.
Future Considerations in PCB Design Software
As the technology continues to mature, several future considerations need attention:
- Increased Automation: Expect more tools to incorporate machine learning and automation features, which can assist in eliminating common design errors.
- Enhanced Collaboration: The integration of collaborative platforms that allow multiple stakeholders to work on PCB designs in real-time will become more prevalent.
- Focus on Sustainability: With an increasing emphasis on sustainable practices, software may evolve to include functions that optimize designs for environmental efficiency.
Monitoring these trends and understanding their implications will empower businesses to remain competitive and innovative in PCB design.